SORALUCE Vertical turning masterclass and milling & boring EXPO 2015
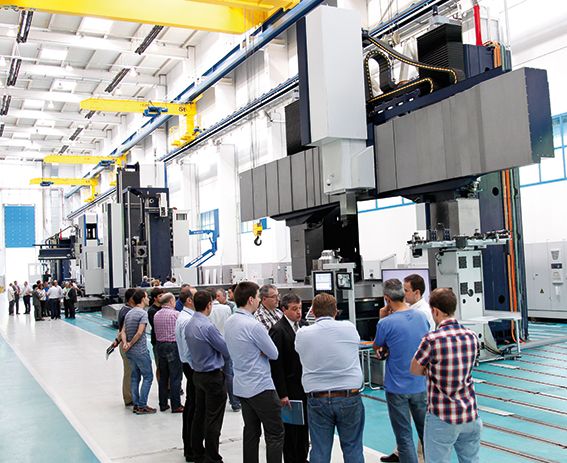
Over 50 guests from 8 countries attended the SORALUCE Vertical Turning MASTERCLASS and Milling & Boring EXPO 2015 held from 7th until 10th July 2015 at SORALUCE manufacturing facilities in Spain.
The event succeeded in showing the highlights and advantages of SORALUCE’s Vertical Turning technology, both with a MASTERCLASS conducted by Xabier Mendizabal (R&D Director) and a hand on experience with the new VTC-6000-H that was showcased during the event.
The Milling & Boring EXPO 2015 provided and insight of SORALUCE technology possibilities with several references on display in machine set-up or advanced assembly process.
The new VTC-6000-H, to be supplied to a shipbuilding corporation, was the star of the event not only for its size but also for its technical capabilities and precision.
On a continuous challenge of innovation, the SORALUCE Vertical Turning Centre (VTC) is a world reference that incorporates an optimized design for maximum precision with functional components that allow higher machining times and lower maintenance costs.
The cinematic chain of the SORALUCE Vertical Lathes is designed to work with high torques and powers which results in a high chip removal capacity. The cinematic chain based in pulleys and a reducing of 2 ranges allows transmiting powers up to 105kW with a single motorization, being possible to install two engines on large range machines.
The positioning precision and interpolation functions of the head are guaranteed by one or two servomotors and a central encoder. This C axis system enables high precision and repeatability, ideal for any precision operation. Moreover, to ensure the quality of all machines, SORALUCE performs laser tests in linear axes and manufactured vertical lathes heads.
SORALUCE Vertical Turning Centres are engineered to include the latest innovations of the market to offer highly customized projects mainly in power generation, naval, large precision bearings, mining, valves and general engineering industries.
During the daily Vertical Turning Masterclass, attendees found the answers to the technical challenges. Subjects such as machine specifications, heads, precision and productivity were deeply analysed with the attendees and good advices on how to get the highest profitability in their machining processes were given.
Furthermore, the SORALUCE DAS system (Dynamic Active Stabilizer) modifies the behavior of machine dynamics to stabilize it in all working conditions, thus increasing machining performance by up to 300 per cent was presented nationally and together with the new Heidenhain TCN 640. Both were on display in the multi-function milling turning center SORALUCE F-MT. This machine provides the possibility of manufacturing complex components in one machine, offering remarkable versatility which leads to effective real time saving and the associated cost savings for end users. This compact solution integrates a flexible working area that can be configured to the customers’ needs with one or multiple working stations with fixed tables and rotary tables usable for both milling and turning operations.
These multi-function machines can complete all operations in a single setup – turning, milling, boring, drilling, tapping – on very intricate parts for industries such as the aeronautical, energy and precision engineering both for unitary and serial production.
The machine is provided with high dynamics: 45 m/min of axis speed with an acceleration of 2 m/s2 in each individual axis. This, combined with the high power and torque of the main spindle and the improved thrust forces in all axes (up to 16 kN), results in a state-of-the-art solution for high chip removal capacity and stable cutting conditions for both milling and turning.
The integrated rotary table, with built-in drive technology, can be used in both milling and turning working modes. With a maximum diameter of 1600 mm and a maximum working load of 8000 kg, this rotary table has a maximum rotational speed of 250 rpm and a maximum turning torque of up to 2500 Nm, supported by a maximum tangential torque of up to 26000 Nm in clamped condition.
For the turning operations, the F-MT incorporates an automatic system for automatically loading / unloading the turning head outside the working area. This turning head is attached to the main body of the milling head of the machine, giving the capability for high chip removal during turning operations as well as precise machining whilst the bearings of the head remain completely protected.
SORALUCE is the division of DANOBATGROUP worldwide reference in milling, boring and turning technology. Throughout its 50 years of history it has continuously made innovative and pioneering contributions in engineering that have become industry standards. Customers recognize SORALUCE for its expertise in solutions guided to improve customer’s efficiency and productivity and for its technological capacity to customize each product based in the customer’s individual needs, likewise generating turn-key projects, designing and setting up complete lines according to quality, efficiency and cost parameters required by the investor.