DANOBAT VG 1000/700 grinding centre to showcase at EMO 2013
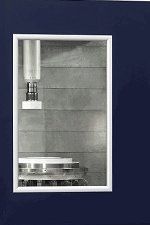
Machining precision and quality are especially important for DANOBAT, for which R&D is being continuously carried out on the machines. The VG range is evidence of this, vertical grinding machines that stand out due to their modular design and different configurations that provide solutions to the specific and increasingly demanding needs of the customer. The different grinding heads, the turning option and the measurement techniques make the VG range the perfect solution for machining of medium and large parts that require high precision, such as stators, gears, aircraft engine bearings, etc. All the VG series models are made up of a configuration of independent slides fitted on linear guides with a high precision recirculating roller system. The cross slide houses the rotary B axis. Both slides are driven by two spindles mounted in tandem with independent servomotors. This system has been chosen to optimise the most demanding dynamic behaviour required for the generation of forms or diamond dressing by high precision interpolation. Both slides are equipped with linear encoders that control the movement and positioning of the slide.
The machine structure has been optimised by means of finite element calculations to achieve the best distribution of the internal ribs, and thus attain the necessary stability to ensure optimal finish quality and precision. The VG 1000/700 model will be exhibited at the EMO 2013 DANOBAT; this is a vertical grinding machine capable of machining components of up to 1000 mm in diameter, 700 mm in height and 3000 kg in weight. The table that is directly mounted on a constant pressure hydrostatic bearing that ensures an excellent surface finish. The VG vertical grinding machines offer the option of adapting an arm for hard turning together with a Hirth locking system; these provide the unit with the rigidity and stability required to be able to achieve high precision turning. In order to reduce the cycle time of a part, DANOBAT offers various automation options for the machine such as the incorporation of a robot for tool changes, an automatic balancing system or a pallet clamping system and external preparation station. The automatic balancing system allows the machine to establish the location of the masses on the wheel head in order to correct the imbalance error and thus achieve an excellent surface finish, while the pallet clamping system and intermediate station reduces the part preparation time within the machine. This system consists of two tables located outside the grinding machine, one for centring and correct positioning of the part and the other for unloading the pallet from the machine once the part has been machined. The system minimises the set-up time on the machine, and ensures that the centring set-up carried out outside will be effective, thus increasing the machine time available for machining.