Top level cylindrical grinding technology
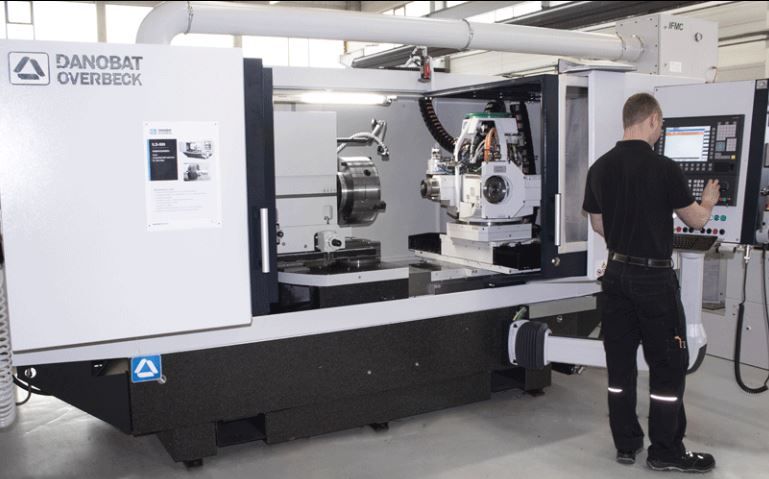
Grinding is one of the most important methods used for the industrial forming of workpieces. Its advantages are the high precision of the pieces created and the excellent quality of surfaces. In addition, it is ideal for the machining of different materials, from steel for tools or plastics to materials of maximum hardness, like ceramic materials or diamonds. This likewise means that the machine tools used conform to particularly high precision requirements. In the sector, we usually joke about having to split the µ. We spoke to one of the leading manufacturers.
“We manufacture grinding machines complying with the most demanding specifications”, says Josu Tornay, managing director of Overbeck GmbH in Herborn. Since 2002, this family business with a long tradition has been part of the Spanish tool manufacturer Danobat. It specialises in the production of high-precision machine tools for internal and radial grinding, catering for industrial sectors whose products require maximum precision and finishing. Its machines are used for machining spindles for machine tools, bearing rings, gear parts, dies and transformation tools, as well as hydraulic valves and pistons, all of which require a µm level of precision. To meet these standards, the design of all these machines seeks to ensure the highest possible accuracy. This starts with the machine bed. It generally consists of a block of solid granite which has been subjected to precise grinding.
This element ensures maximum mechanical and thermal stability, as well as high vibration absorption.
Temperature control of the internal space, which is so important for high precision, is provided by a heating-cooling system which maintains temperature of the most important parts within strict temperature ranges. This attention to detail is likewise reflected in other aspects, such as, among others, the parallel alignment of the guides or the incorporation of measuring bars into the different assemblies. Special attention is likewise paid to the work heads, which are mounted and checked thoroughly in a special room that is thermally controlled. The concentricity is likewise established and recorded for each of the heads, and they undergo a fatigue test. A similar procedure is carried out in the case of the external grinding wheel heads and dressing heads. In addition, the two main rotary axes (B0, B1) are mounted in the plant itself and are subjected to strict fatigue tests.
Optimising profitability for the user
“The best way to attract and keep clients is to provide them with solutions that help them establish themselves in the market”, adds J. Tornay. To this end, he says that it does not suffice to sell “standard” machines, no matter how good they are as individual machines. What matters is to discuss the client’s specific needs and follow with an optimised solution in the shape of a complete and customised package. According to Tornay, his business group aims at tackling these projects together with the client, while contributing its broad technical knowledge. In this process, for every solution foreseen, an analysis of the necessary variations is carried out, such as special versions of the machine and its automation, with handling systems, for example, as well as adaptation to prior or subsequent processes so that, if the client so requires, a turnkey installation is possible. In certain spheres of application, such as tool building, it likewise comprises mature, user-friendly software, additional special software modules, such as those to help set the parameters of frequent types of contours. Specific solutions are developed with the aid of the know-how of the Danobat Group’s R&D centre.
Tornay adds that this work in collaboration with the client continues once the machine has been delivered and commissioned, thanks to a solid Technical Support Service available throughout the world. In this respect, service packages adapted to the client’s specific needs are likewise offered. In addition to the Technical Support Service and conventional mechanical reviews, the client is also offered control software upgrades or the integration of more advanced standards in technology and safety.
ILD series universal internal grinding machines...
“The new ILD series implies the expansion of our range of internal universal grinding machines”, explains Jens Peters, project manager at Danobat Overbeck. The new machines allow for internal, external and surface grinding of large parts up to 1,300 mm long (incl. clamping system) with diameters of up to 760 mm, all of which guarantee maximum precision. The ILD 500 is the classic model for applications like grinding spindles, spindle housings or tools, for example, for production machines. It convinces above all because of the length of its part holder and its B0 axis adapted to these applications. The rotary axis in all models of the ILD series allows for precision grinding of conical surfaces as well as automated cylindrical corrections, without the need to mount a specifically dressed wheel or resort to interpolation. As the wheel moves along one axis, no “jagged edges” are formed, which is inevitably usually the case. In addition, the entire width of the wheel is utilised in a uniform way.
For clamping large pieces, ILD machines have a W axis which can be moved manually or by a motor. They are designed to hold a turret with 4 spindles as well as an integrated measuring probe and up to five dressing systems.
The measuring probe, with the help of the control software, is of special importance, as it enables continuous supervision of the process without the need to remove and re-clamp the piece. This even allows for the detection of minimum modifications to the dimensions of the wheel as well as the corresponding corrections in the CNC programme with no interruption whatsoever.
The ILD 600 is to be presented as a new development at the EMO 2017 in Hannover This type of machine is characterised by a prolonged Z axis and a 3-position dressing turret. This completes the offer of universal internal grinding machine for pieces with bore of up 400 mm. deep. At this venue, the company will also present a new design for a machine, comprising, among other things, a 19” panel.
The new ILD 700 & ILD 700 U models...
These new models of the ILD series allow for the internal, external and surface grinding of large pieces such as ball bearings rings or aeronautical parts with dimensions of up to 500 mm. long (incl. clamping system) and 760 mm in diameter, all of which guarantee maximum precision. Its design takes into account its maximum flexibility in use.
Thanks to the additional U axis, it enables the use of up to five different dressing systems without affecting the full use of the machining area. The U axis works in such a way that this additional slide allows the piece to be removed from the machining position so that the dressing tools can be used unhindered. This ensures continuous operation even with changing tasks, without the need to make any adaptations to the machine and, as a result, with no time loss.
This concept convinced at the outset, and even at the project stage, the first client bought the system in a “pack of 4”. This, according to J. Peters, clearly reveals the great trust placed by the client in Danobat Overbeck. The spheres of applications are above all the manufacture of large internal and external rings for special bearings in small to medium runs with maximum quality requirements. In addition, in this case, special aspects such as specific geometries, special materials (ceramic) and different clamping systems need to be added.
...and the IRD 400 internal and radial grinding machine
"The IRD series with models 200 and 400 is particularly suitable for machining dies and transforming tools”, explains J. Peters. One of its peculiarities is the B0 axis which, with rotations of up to 91º, allows for high precision surface grinding even of front surfaces. Thanks to the precise control of axes, even complex internal contours can be made using one profile wheel and one contour path. In this model too, the 4-spindle turret includes a measuring probe integrated in the NC software, with which the starting position of the workpiece as well as the real value of the excess still existing can be detected. This ensures that on the final finishing run the system reaches the required measurement with precision. In round contours, roundness deviations of 0.5 µm. can be reached.
Another of the peculiarities is the high degree of exact synchronisation of all the movements of the axes, including the rotation axis of the workpiece (C0), so that an eccentric grinding of the workpieces can be carried out. At the same time this means that complex geometries can also be machined in the piece using coordinate grinding, enabling the manufacture of square, rectangular or free form shapes with great precision.
Machine bed consists of a solid precisely grinded block of granite
Complementing a LG 200 external grinding machine for the client’s specific subsequent process, including handling by robot
In IRD models, the B0 axis allows a rotation of up to 91 º. This enables the surface grinding with maximum precision of front surfaces also
Precision grinded dies in the IRD 400, for use in transformation processes
Load capacity: The work head of the ILD together with the workpiece can be 1,300 mm. long and 500 kg. The maximum diameter of the workpiece is 760 mm