Talleres Allus opts for DANOBAT for large part machining
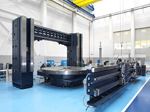
Talleres Allus, a company devoted to large part precision machining, has put its trust in Danobat for the turning and milling of large parts in sectors such as offshore-wind, oil, aerospace and capital goods. We are dealing with a multifunction vertical lathe VTC-8000-H, an extraordinarily large machine, unique within the large machining sector.
The main structural elements are made from stabilised cast iron that prevent vibrations and ensure maximum stiffness and stability of the machine. With a total weight of 220,000 Kg, this turning centre can accommodate parts of up to 150 Tn, 8000 mm in diameter and more than 4000 mm in height. Because of the vertical displacement of the cross rail, both short and very long parts can be machined with the highest quality and precision in any position of the cross rail. The machine, equipped with the most advanced technology, uses hydrostatic technology in the following areas:
- Hydrostatic slideways are used on both the X and Z axis.
- The table is supported radially and axially by hydrostatic elements.
The machines' hydrostatic head is opearated by two 105 kW motors with a torque of 170,000 Nm. The Talleres Allus vertical lathe is equipped with two motor-driven RAMs, which enable turning and milling in two axes at the same time, providing a significant reduction in operating times. The cross section of each RAM is 300 mm and they have a vertical outlet of up to 2500 mm. Each RAM incorporates a TV camera so that the operator can see the operation being carried out in real time. The machine incorporates a double C axis, as well as two tool magazines, one for each RAM, with many positions for turning, drilling, threading and milling tools, as well as for straight and angular heads that require these tools, the result is a totally automated machine. The machine has a lift attached at the side for use when very tall parts are being machined. Great care has been taken with the ecological design of the machine, consumption of oil has been minimised as far as is possible, and there is a special emphasis on energy saving through the use a 'sleep mode' programmable system. The installation of this lathe will enable Talleres Allus to take a major step forward in attracting new customers as its implementation will make it possible to finish any large part in a single machine, without having to carry out the operations on different equipment as has been the case up until now, and a high level of parallelism and perpendicularity is ensured.