Copper Alloys has invested in DANOBAT band saw machines
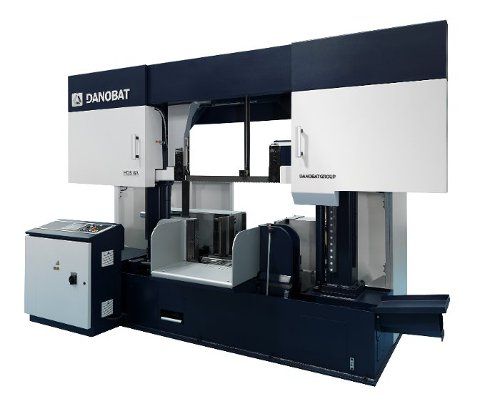
Aluminium/bronze billets are cut up to four times faster than previously possible.
As a leader in copper and nickel based alloys, supplying forgings, castings and components to engineers around the world, Stoke-on-Trent based Copper Alloys Ltd are renowned for their particular expertise in the defence, aerospace and petrochemical industries, supplying precision engineered products for use in many diverse applications principally in the marine environment, from oil rigs to nuclear submarines.
After encountering speed and accuracy difficulties with an existing production bandsaw, Managing Director John Dudley knew exactly who to call to solve the problem, having previously purchased two DANOBAT bandsaws from Prosaw for similar applications.
The process in question involves cutting cast aluminium/bronze billets of up to 810mm in diameter. The billets are cast adjacent to the cutting facility, to where they are transferred on cooling.
The machine specified by Prosaw is a DANOBAT HDS 8A bandsaw which has the capability of an automatic feed system which automatically positions the billets in the correct location for cutting following each completed cut, meaning that continuous production is possible. This is an important upgrade on the previous system as the DANOBAT machine requires little or no operator interaction and is reliable enough to operate automatically for 24 hours each day.
The Company’s standardisation of DANOBAT bandsaws has a further advantage in that all three DANOBAT machines now operate using the same programme, leaving the operator free from the necessity of reprogramming.
Commented Managing Director John Dudley “We purchased our first DANOBAT machine from Prosaw ten years ago and have always been delighted with the quality of the machines and of the excellent service provided by Prosaw. The replacement of our previous machine with the DANOBAT 800 means that the improved speed and straightness in cut that this machine achieves will increase our yield and significantly reduce the risk of producing scrap products.”