Caso de éxito: Mecanizado de precisión para el proyecto aeroespacial MetOP
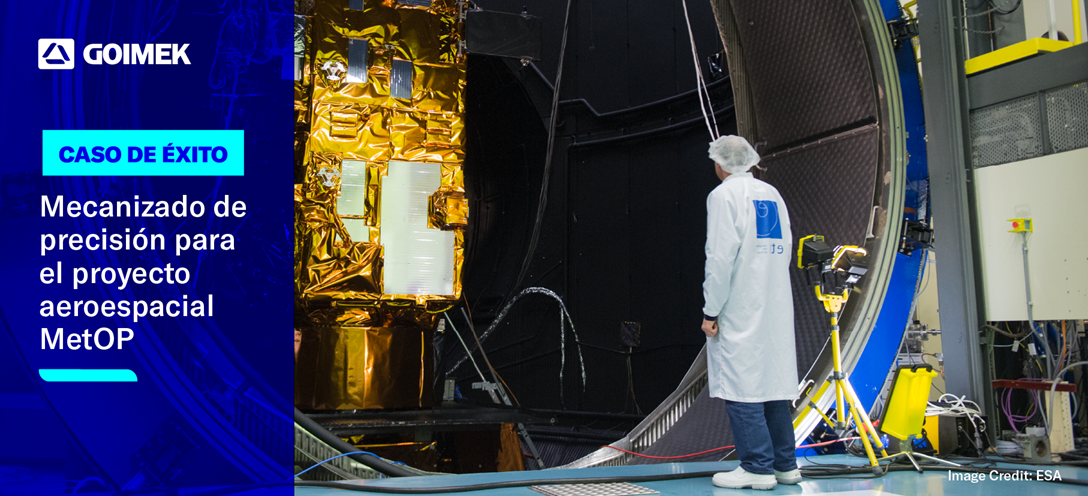
-
Goimek, especialista en el mecanizado de precisión perteneciente a Danobatgroup, participa en la misión con un amplio número de piezas con geometrías complejas en materiales exigentes: titanio e inoxidable
-
El secreto de su éxito reside en la capacidad de gestionar los procesos más allá del propio mecanizado, desde la cadena de suministro, pasando por la documentación, hasta la validación del premontaje
Goimek atesora más de 30 años de experiencia en el sector aeroespacial. Un largo bagaje en el que ha sumado infinidad de proyectos complejos para el mecanizado de piezas destinadas a misiones espaciales. Este caso de éxito, en el que ha trabajado para el cliente OHB Italia S.p.A., es tan solo un ejemplo de la capacidad de la compañía para dar respuesta a los retos más exigentes.
La misión MetOP cuenta, actualmente, con dos satélites que ofrecen información detallada de la atmósfera, océano y tierra firme, con la que es posible realizar previsiones meteorológicas fiables con hasta 10 días de antelación, todo un hito en este este campo. En los próximos años se prevé ampliar la misión, añadiendo otros seis satélites más a la órbita.
Mecanizados de precisión
El proyecto fue encargado por OHB Italia S.p.A, una de las tres compañías aeroespaciales líderes en Europa. Goimek se encargó del mecanizado de precisión de las piezas de bloqueo del espejo de un radiómetro de microondas, un sistema que, actualmente, forma parte del Instrumento MWI para la misión MetOP. Este mecanismo permite mantener sujeto el espejo durante el lanzamiento del satélite hasta que es desplegado en su órbita. En ese momento, ese mismo elemento se encarga de liberar el espejo para que pueda girar sobre sí mismo y, así, transmitir la señal correspondiente durante toda la vida útil del satélite.
Materiales altamente resistentes
El proyecto requería de materiales altamente resistentes a las condiciones del espacio.
- Titanio: Es el material más utilizado en el proyecto; la mayor parte de la estructura está hecha de titanio. La razón de su elección es su excelente relación entre peso, resistencia mecánica y resistencia térmica. Y es que, estas características lo convierten en el material perfecto para resistir las extremas temperaturas del espacio. Además, la utilización del titanio para el mecanizado de piezas de precisión ofrece una ventaja muy importante, sobre todo para el sector aeroespacial: gran resistencia mecánica con un peso relativamente bajo. Un factor fundamental, dado que llevar un kilogramo al espacio cuesta alrededor de 60.000$.
- Inoxidable: Las piezas de inoxidable que se fabricaron para el Instrumento MWI fueron destinadas al mecanismo que bloquea y libera el espejo del satélite. De esta manera, se consiguió aportar mayor resistencia al desgaste derivado del rozamiento de las piezas.
Un servicio integral
A pesar de la complejidad y extrema exigencia del proyecto, Goimek afrontó el proyecto con la seguridad que aporta haber dado respuesta a decenas de retos para el sector aeroespacial. Su amplio bagaje como especialistas en el mecanizado de precisión permitió al equipo brindar un servicio integral.
El primer paso fue la cadena de suministro. Los materiales aeroespaciales requieren de certificaciones específicas y la gestión de acopio de los mismos, procesos en los que Goimek cuenta con mucha experiencia y conocimiento, además de capacidad de adaptación a cada situación.
El mecanizado de materiales duros fue el eje central del proyecto, a pesar de que el resto de procesos adquirieron, también, especial relevancia para el éxito de este. Tanto el titanio como el inoxidable son altamente exigentes durante su mecanizado ya que, entre otras dificultades que presentan, tienden a adherirse a las herramientas que arrancan el material. Además, la complejidad aumenta cuando se trata de piezas de espesores muy bajos porque producen vibraciones. No obstante, el equipo de ingeniería aunó fuerzas con el de calidad para diseñar un proceso de fabricación específico para cada una de las piezas. Un proceso que, además, debía ser estable y robusto para garantizar la geometría del mecanizado.
La trazabilidad y gestión documental también formaron parte de este caso de éxito. Y es que el sector aeroespacial requiere de piezas documentadas:
- Procedencia y composición material
- Certificados de los tratamientos térmicos y superficiales
- Registro de las mediciones
- Informes de control detallados
- Dossier de la elaboración de cada pieza
El éxito en este tipo de casos reside en el conjunto de todos estos procesos, llevados a cabo con total precisión y profesionalidad, pero factores como la capacidad de adaptación juegan un papel fundamental. Esta es una característica inherente a Goimek y este caso lo refleja de manera fiel. El cliente necesitaba comprobar el correcto funcionamiento del mecanismo antes de recibirlo en sus instalaciones. Por ello, el equipo participó codo con codo con el cliente en la validación y premontaje de los equipos, una tarea que permitió identificar ciertas mejoras en el diseño.
Cabe remarcar que ni este ni ninguno de los trabajos anteriores con clientes del sector espacial hubieran sido posibles sin la certificación EN9100 con la que cuenta Goimek. Este certificado lo valida como fabricante de piezas que serán enviadas al espacio exterior.
Conoce más acerca del mecanizado de precisión de elementos aeroespaciales, pincha aquí.
Sobre Goimek
Goimek es una empresa especializada en mecanizado de alta precisión y grandes mecanizados ofreciendo soluciones integrales y especializadas a clientes de sectores como el aeroespacial, máquina-herramienta, generación de energía y bienes de equipo. La compañía forma parte del grupo empresarial Danobatgroup e integra todas las necesidades de la cadena de aprovisionamiento de las piezas mecanizadas desde la compra de la materia prima hasta la verificación y certificación de las piezas mecanizadas.
Sobre Danobatgroup
Con una trayectoria de 65 años en el ámbito de la fabricación industrial, Danobatgroup cuenta con una plantilla formada por más de 1.300 personas altamente cualificadas. El grupo es un agente de referencia internacional en el sector de la máquina herramienta y los sistemas avanzados de producción.