Unique solutions created with and for the customers, that revolutionise the manufacturing processes
With a strong proficiency in grinding, turning, milling, boring, and precision robotics technologies, our leading machine tool and advanced manufacturing companies are at the forefront of designing and crafting solutions tailored for the production of high-value components across the most demanding industries.
Manufacturing technologies
Our offer encompasses a solid and comprehensive suite of multi-technological solutions, including:
-
-
Grinding
-
Milling and boring
-
Vertical turning
-
Hard turning
-
Multitasking solutions
-
Machines for railway wheelsets, wheels and axles
-
Precision robots
-
Grinding
- External grinding machines
- Internal grinding machines
- Centreless grinding machines
- Vertical grinding machines
-
Milling and boring
- Bed type milling machines
- Fixed table travelling column milling machines
- Floor type milling boring machines
- Portal & gantry milling boring machines
-
-
Hard turning
- Horizontal hard turning lathes
- Vertical hard turning lathes
- Hybrid turning and grinding machines
-
Multitasking solutions
- Multitasking milling and turning centres
- Multitasking floor type (milling and turning)
- Multitasking portal machines (milling and turning)
- Hybrid grinding and hard turning machines
- Hybrid hard turning and grinding machines
-
Machines for railway wheelsets, wheels and axles
- Underfloor wheel lathes for passenger trains
- Underfloor wheel lathe for locomotives
- Portal lathe for wheelset reprofiling and brake disc turning
- Wheel borer for wheel hub boring
- Automated wheel boring and wheelset mount cell
- Automated used axle repair & reconditioning cell
-
CNC precision robots
-
DMTR — Danobat high precision robot
-
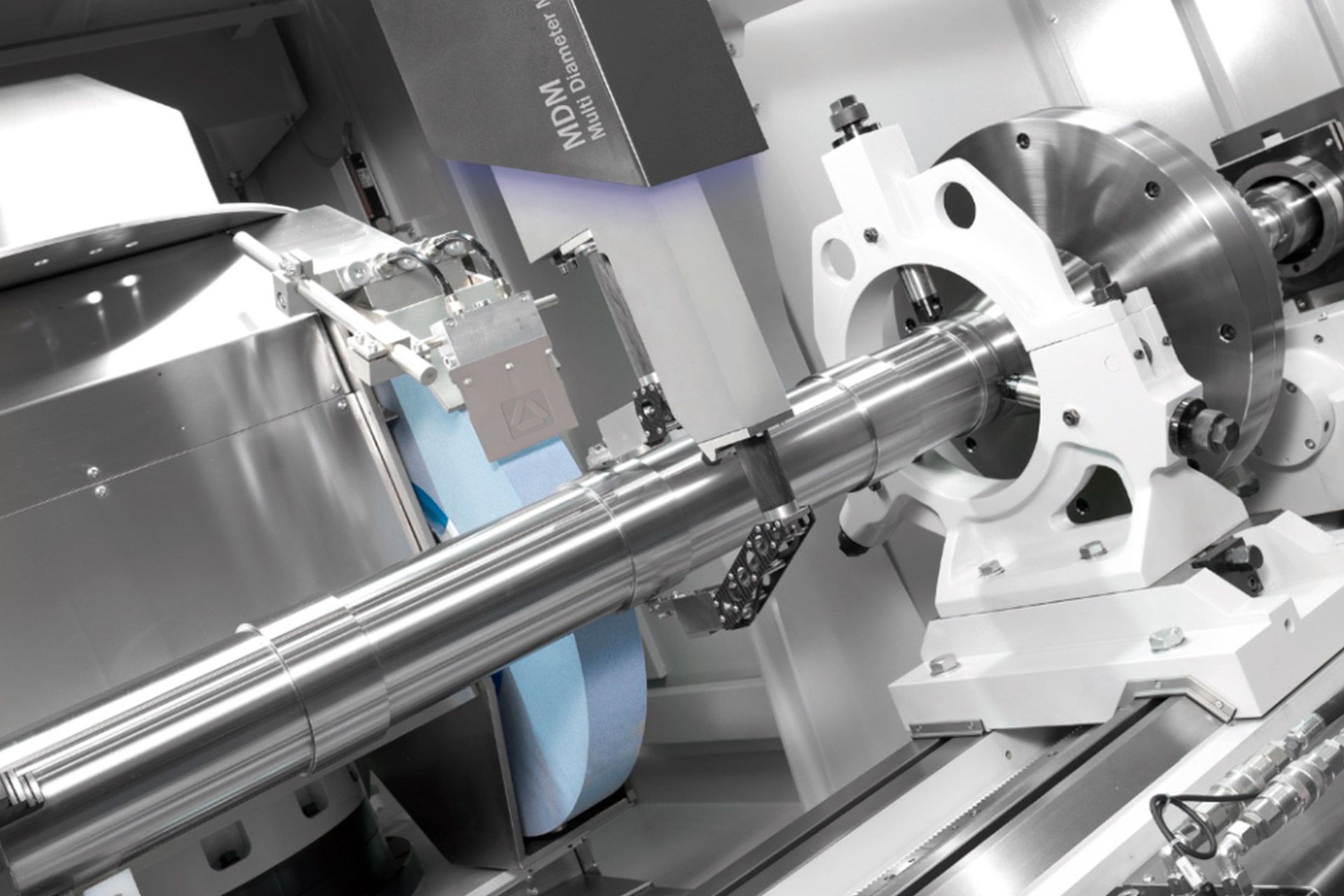
Grinding
- External grinding machines
- Internal grinding machines
- Centreless grinding machines
- Vertical grinding machines
Milling and boring
- Bed type milling machines
- Fixed table travelling column milling machines
- Floor type milling boring machines
- Portal & gantry milling boring machines
Precision turning
- Horizontal hard turning lathes
- Vertical hard turning lathes
- Hybrid turning and grinding machines
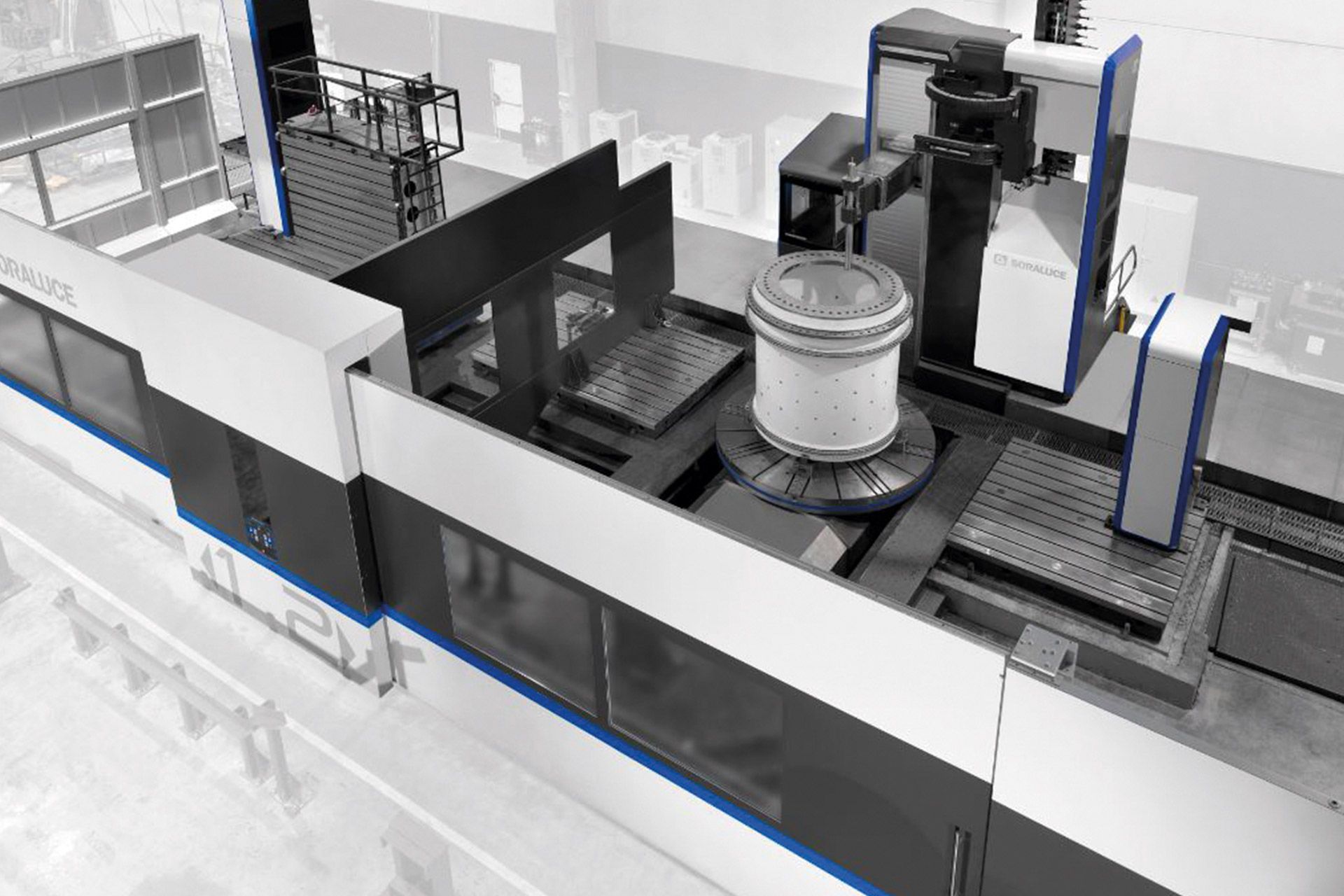
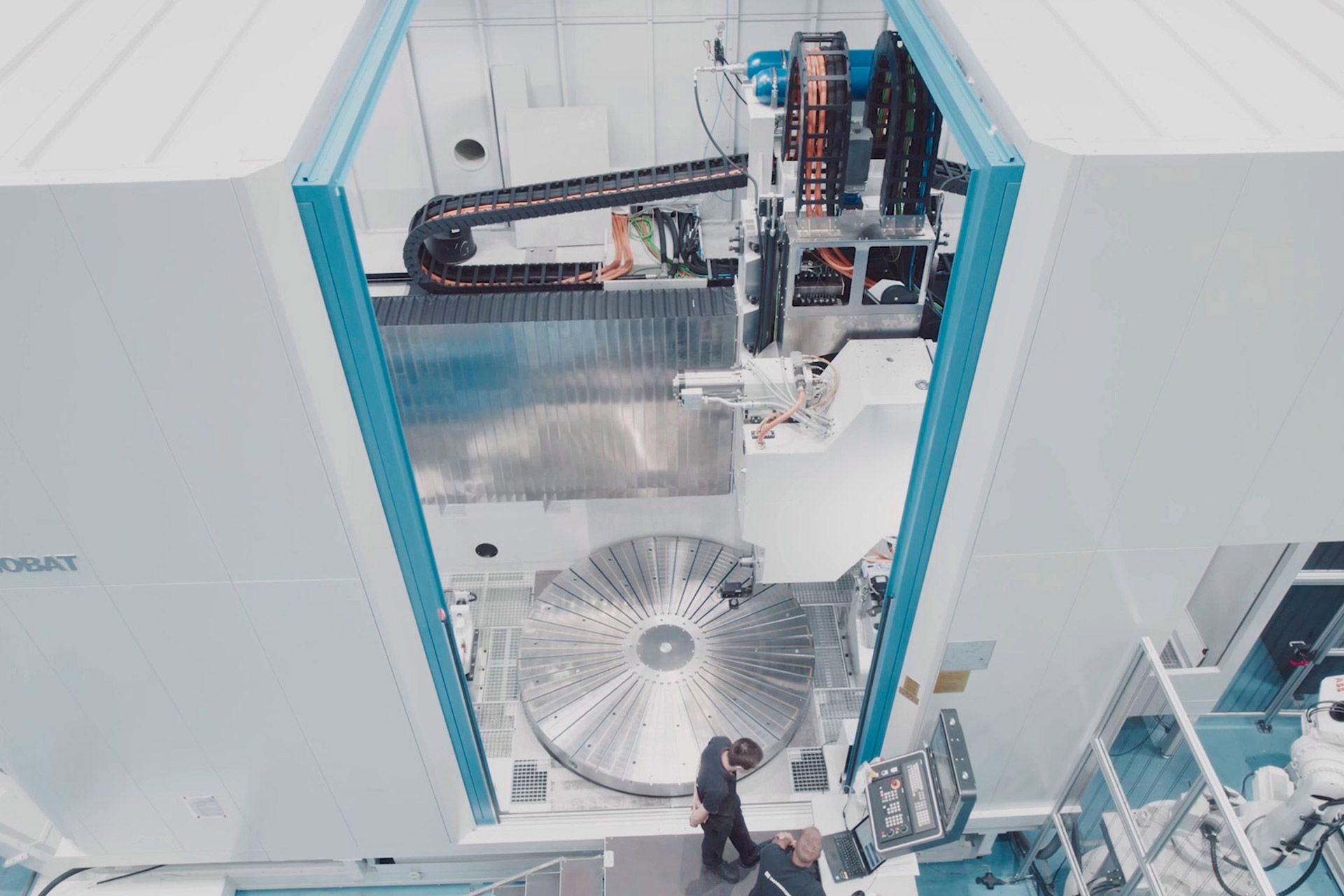
Multitasking solutions
- Multitasking milling and turning centres
- Multitasking floor type (milling and turning)
- Multitasking portal machines (milling and turning)
- Hybrid grinding and turning machines
- Hybrid turning and grinding machines
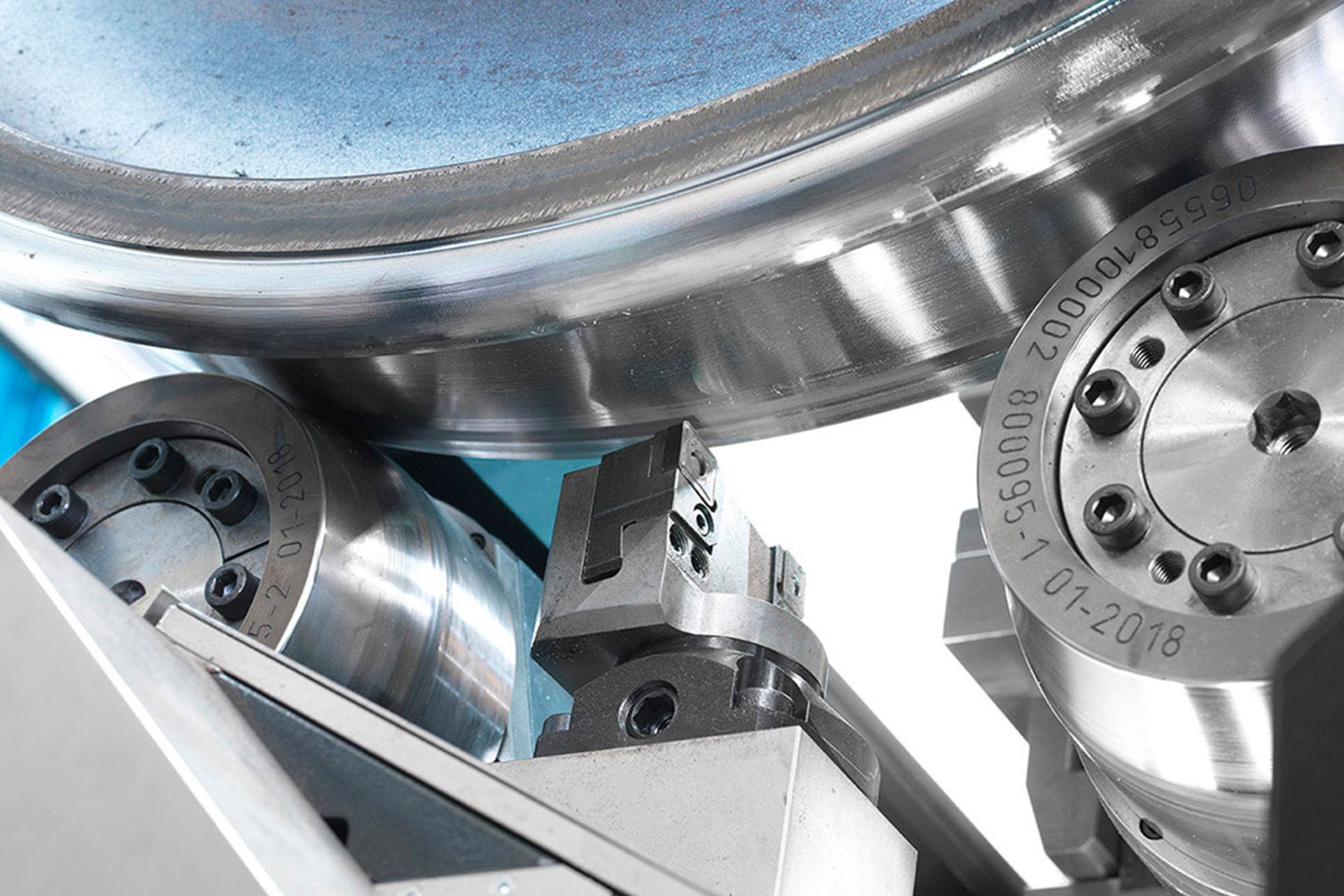
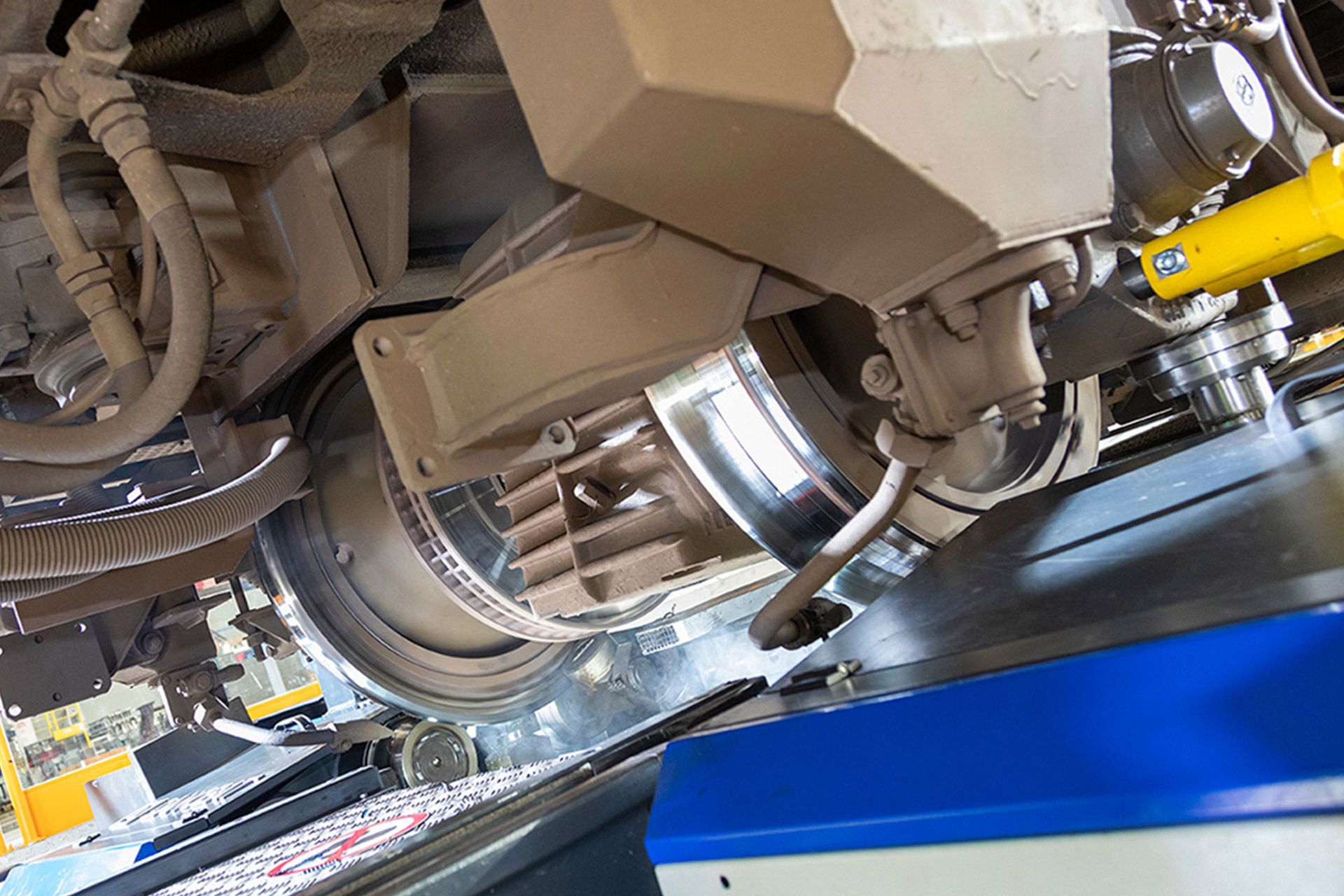
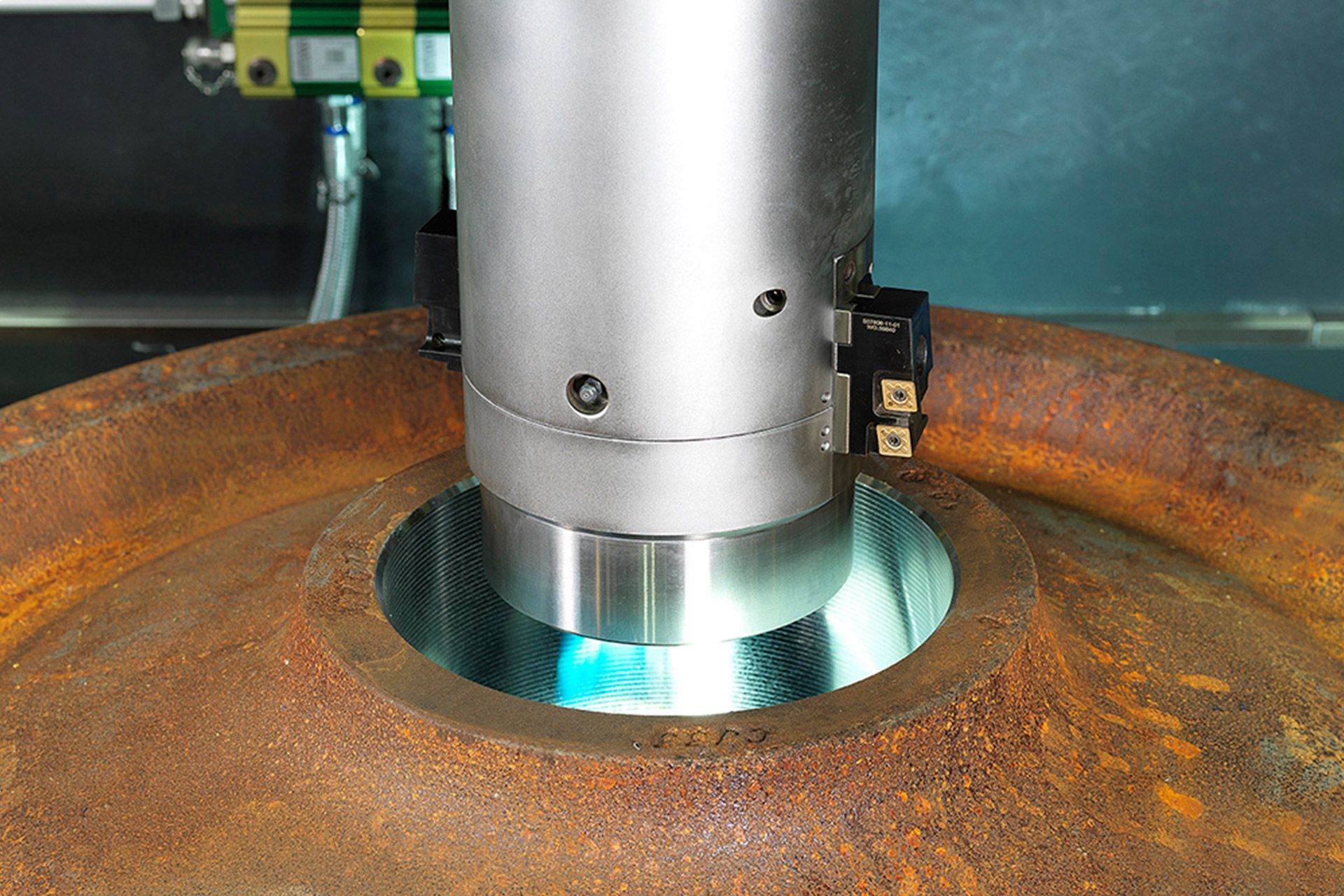
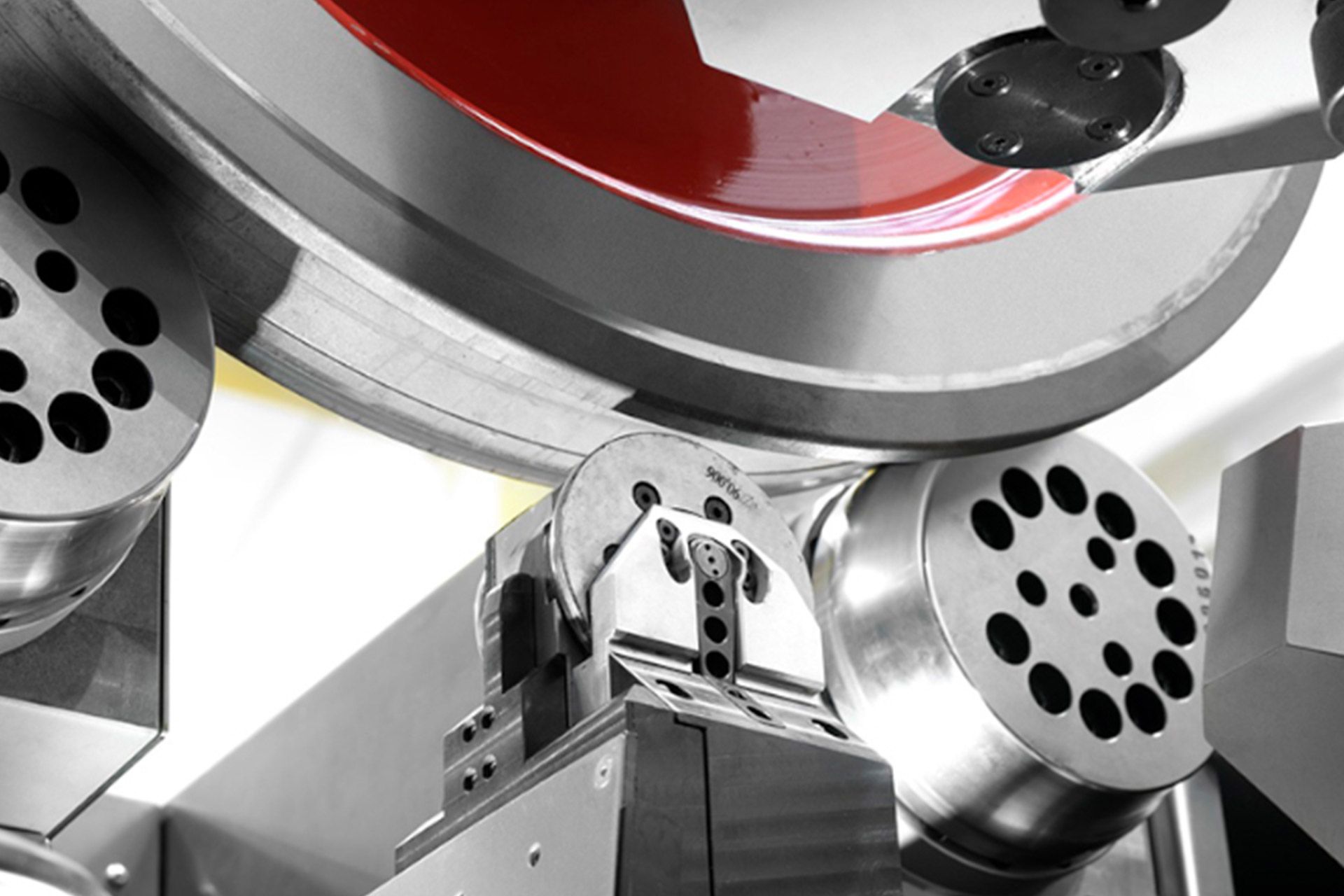
Machines for railway wheelsets, wheels and axles
- Underfloor wheel lathes for passenger trains
- Underfloor wheel lathe for locomotives
- Portal lathe for wheelset reprofiling and brake disc turning
- Wheel borer for wheel hub boring
- Automated wheel boring and wheelset mount cell
- Automated used axle repair & reconditioning cell
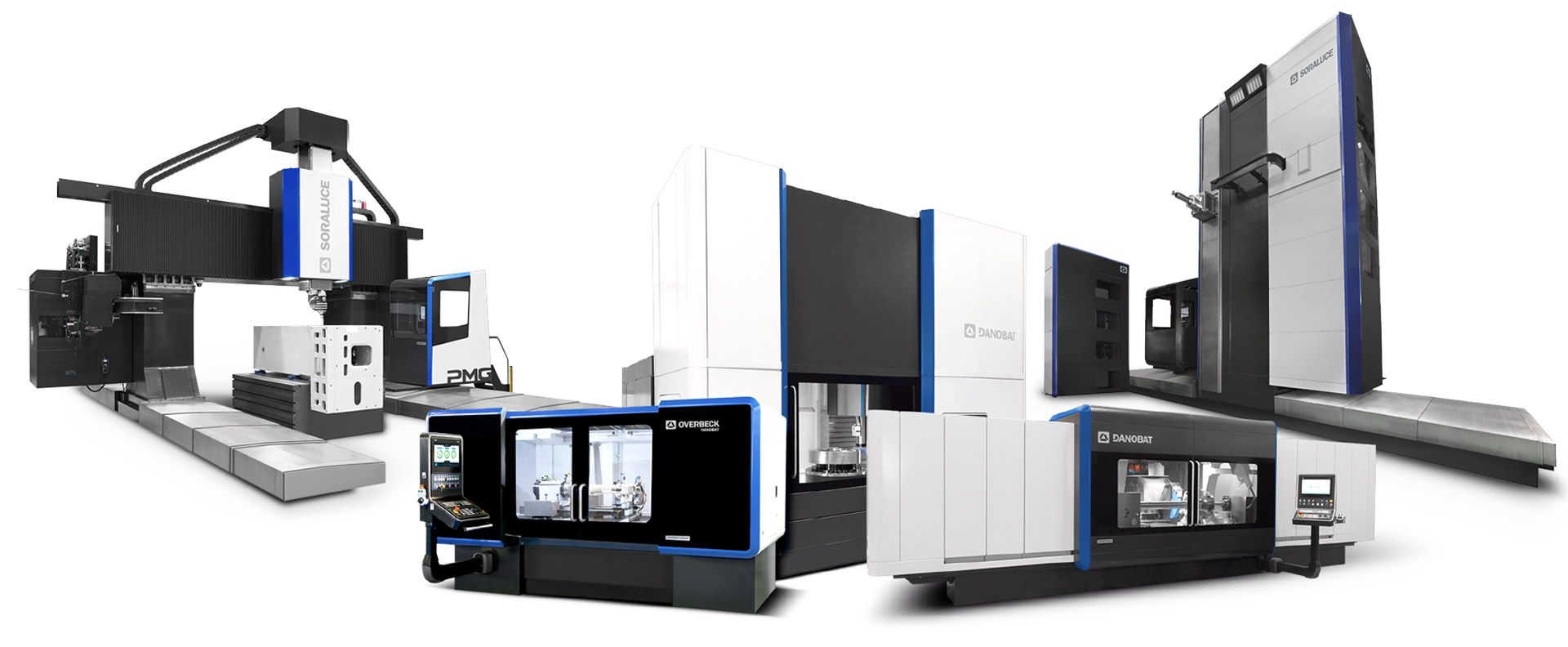
Application solutions
Our solutions are aimed at the manufacture of high value-added components for, among others, the following sectors:
-
Aeronautics and aerospace
In the aerospace sector, staying at the forefront is imperative and for this reason this sector poses significant challenges in terms of manufacturing. The need for lightweight, yet highly resistant components with intricate geometries requires a new approach and innovation in machining processes.
Danobat and Soraluce offer unique solutions for the manufacturing and maintenance of critical components for aircraft, helicopters, satellites, and rockets, including engines, aerostructures, landing gear, and more.
-
Automotive and electric mobility
In the automotive and electric mobility sector, manufacturing components presents diverse challenges. The advent of electric and hybrid vehicles brings the opportunity for a more sustainable paradigm.
Danobatgroup companies have always been industry leaders, developing solutions for automotive component manufacturing in collaboration with leading vehicle manufacturers. This includes applications like camshafts, tulips, gear case shafts, diesel injection pump shafts, steering rack components, moulds for vehicle doors, bonnets, and more.
Faced with this new paradigm, we continue to innovate to address the production challenges of this new generation of vehicles.
-
Railways
For rolling stock and structural materials used in trams, subways, intercity trains, high-speed trains, and freight trains, Danobat and Soraluce provide integrated solutions for manufacturing and maintenance.
The railway sector faces diverse and critical challenges that impact the efficiency, safety, and sustainability of rail transport. One of the key challenges is the need to develop durable components while maintaining high standards of strength and safety. In this regard we are working together with leading manufacturers to create new manufacturing and maintenance solutions that incorporate the latest technologies for applications such as axles, wheels, and bogies.
-
Energy
Danobat and Soraluce offer manufacturing solutions for various components in the energy sector, including renewable energy, hydropower, gas, and nuclear power.
We address specific challenges and requirements arising from the critical nature of equipment used in power generation, transmission, and distribution.
Our solutions demand high precision and stringent tolerances to ensure optimal performance and safety of components that often operate under extreme conditions. -
Capital goods
In a sector where production efficiency and quality are paramount, Danobat and Soraluce deliver advanced solutions for machining high-value-added components in diverse industries such as machine tools, agricultural machinery, mining equipment, food processing machinery, textile machinery, and metallurgical plant machinery.
Our ability to swiftly and seamlessly incorporate technological advances and adapt to emerging trends is crucial for successfully tackling the challenges in this sector.
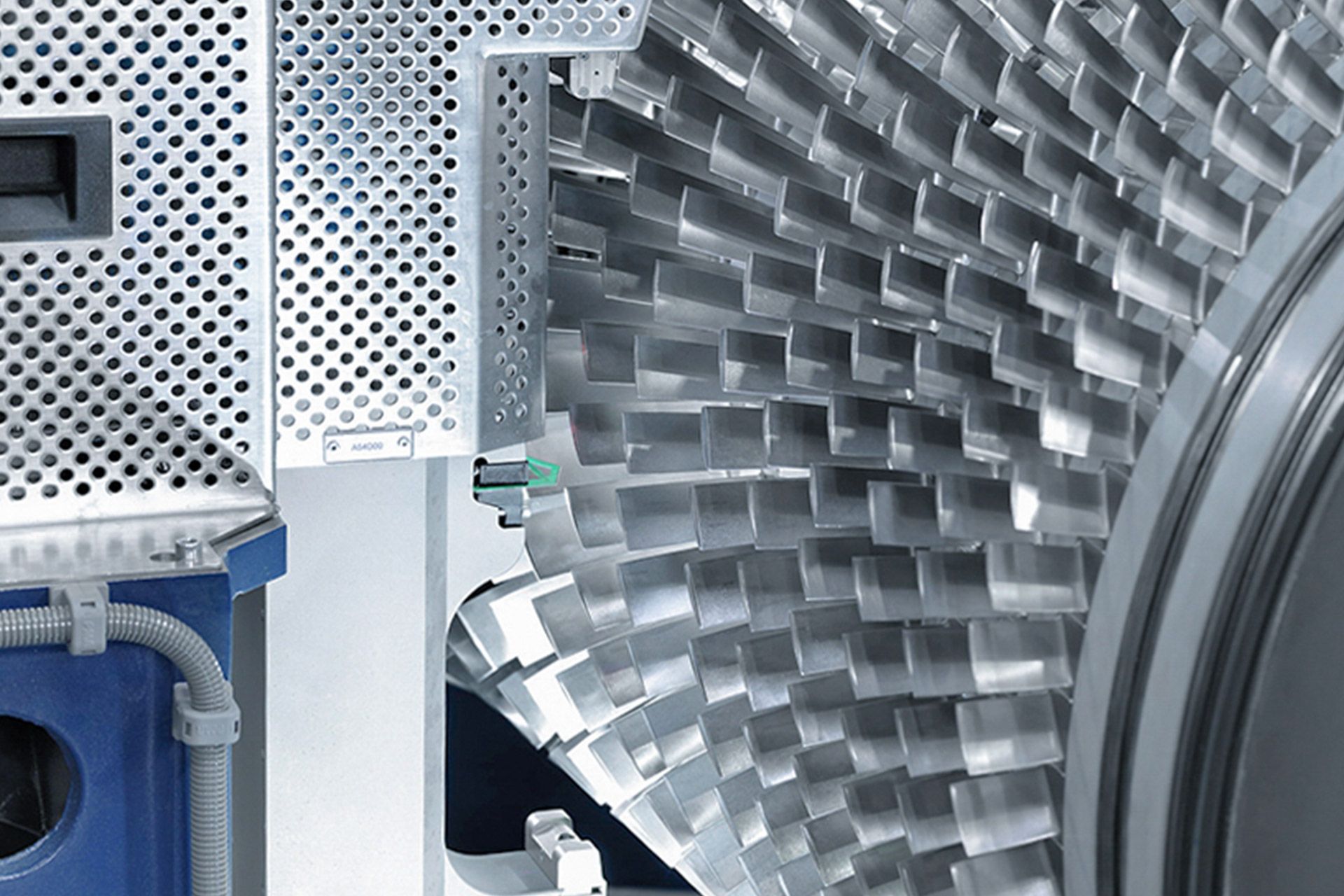
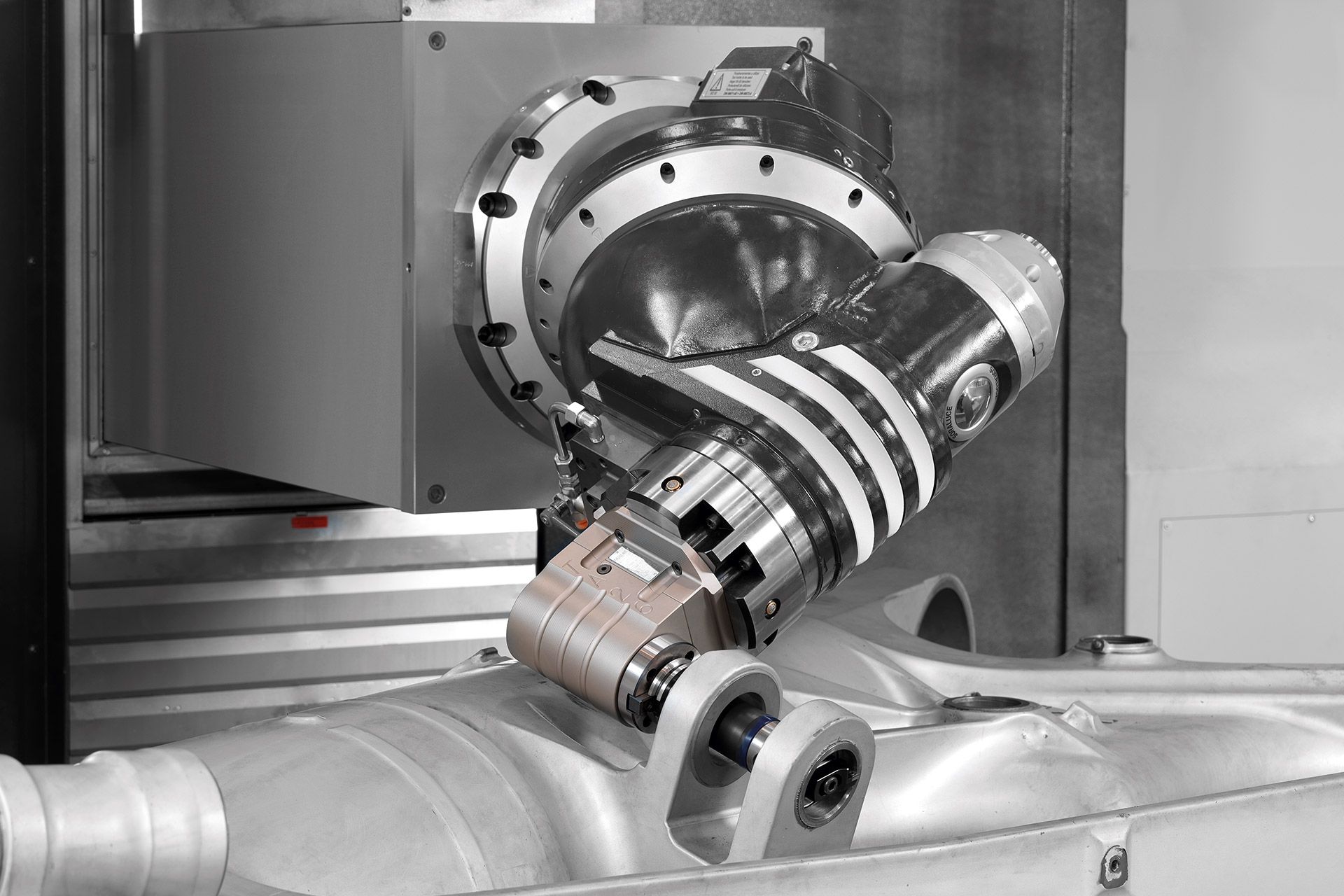
Aeronautics and aerospace
In the aerospace sector, staying at the forefront is imperative and for this reason this sector poses significant challenges in terms of manufacturing. The need for lightweight, yet highly resistant components with intricate geometries requires a new approach and innovation in machining processes.
Danobat and Soraluce offer unique solutions for the manufacturing and maintenance of critical components for aircraft, helicopters, satellites, and rockets, including engines, aerostructures, landing gear, and more.
Automotive and electric mobility
In the automotive and electric mobility sector, manufacturing components presents diverse challenges. The advent of electric and hybrid vehicles brings the opportunity for a more sustainable paradigm.
Danobatgroup companies have always been industry leaders, developing solutions for automotive component manufacturing in collaboration with leading vehicle manufacturers. This includes applications like camshafts, tulips, gear case shafts, diesel injection pump shafts, steering rack components, moulds for vehicle doors, bonnets, and more.
Faced with this new paradigm, we continue to innovate to address the production challenges of this new generation of vehicles.
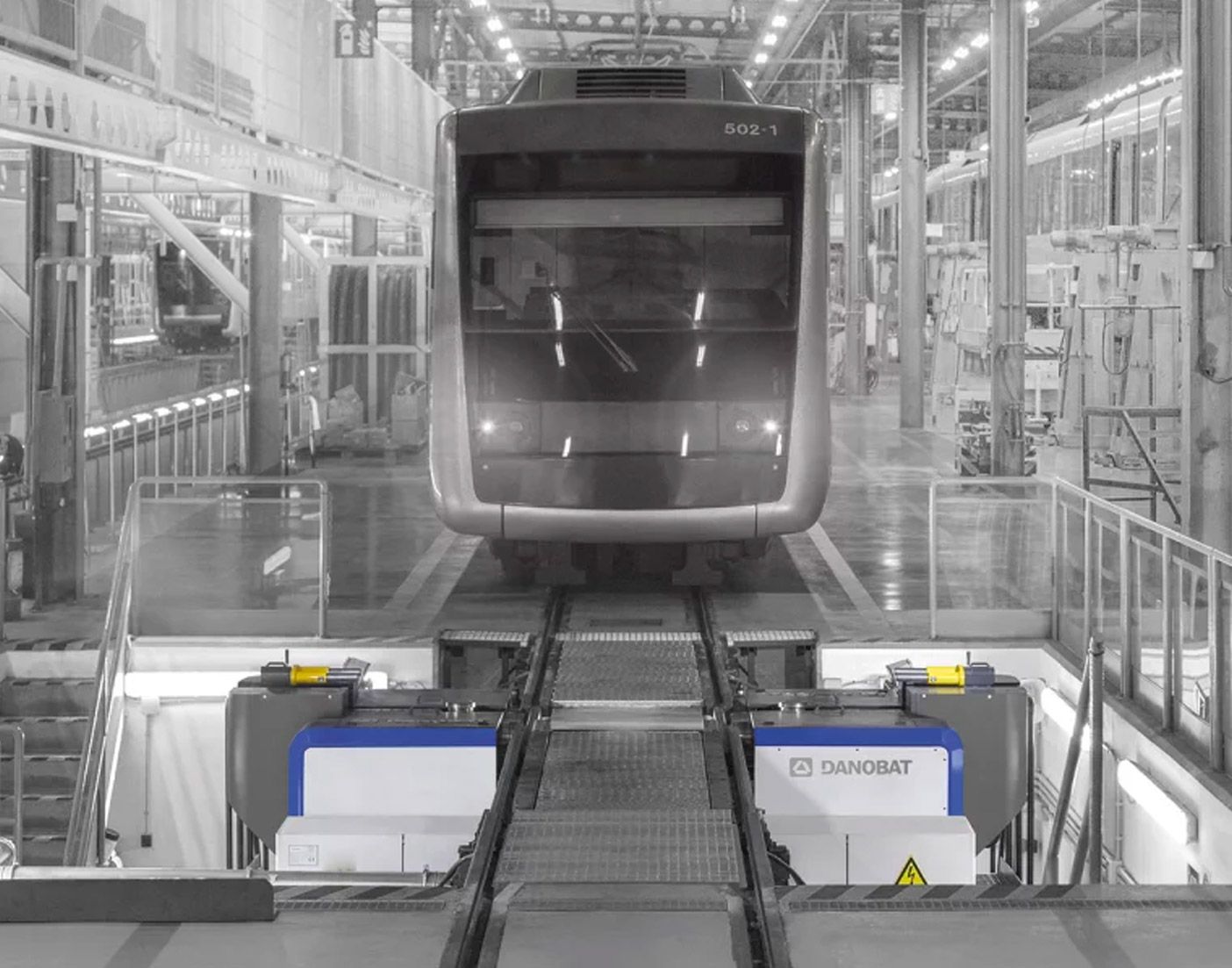
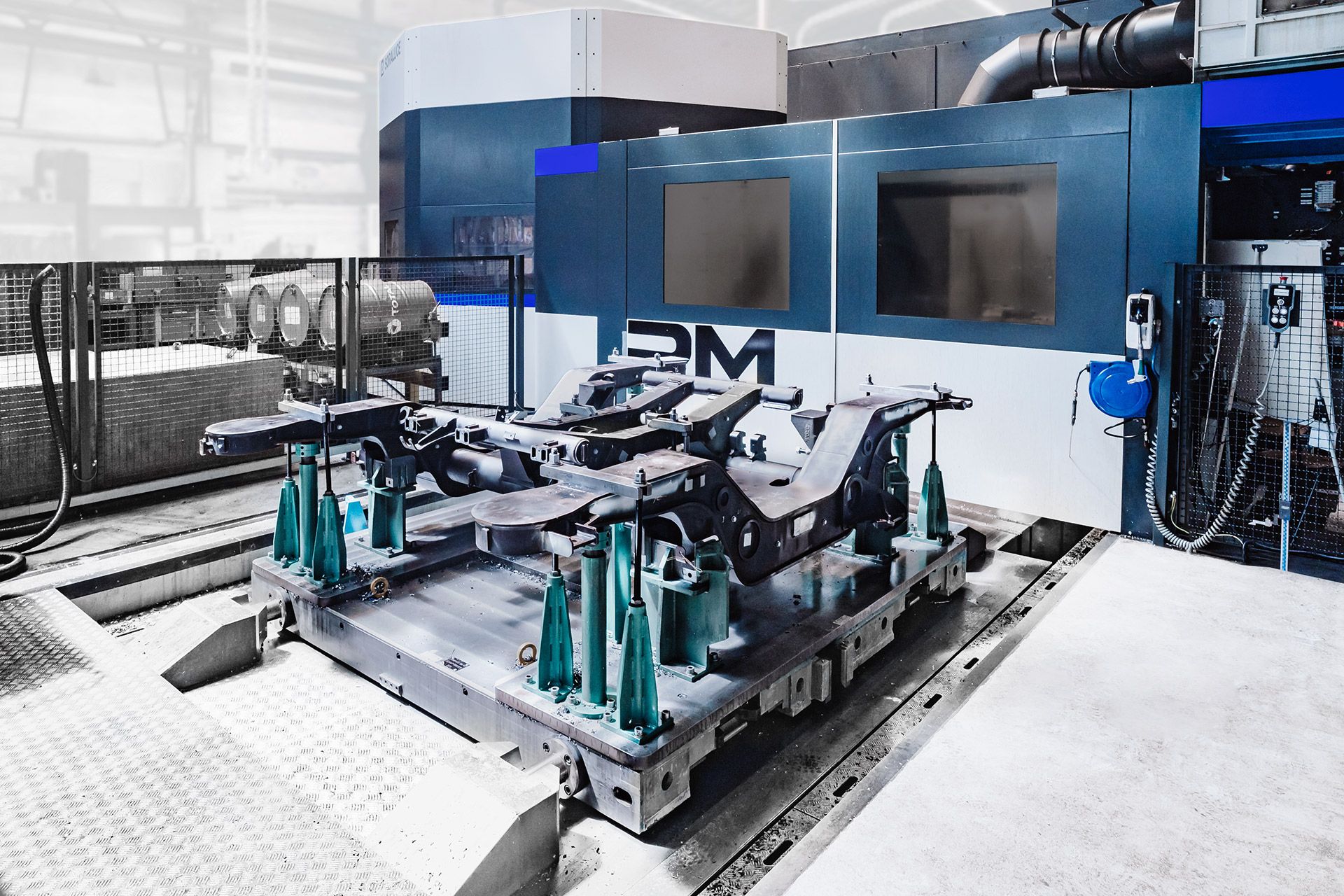
Railways
For rolling stock and structural materials used in trams, subways, intercity trains, high-speed trains, and freight trains, Danobat and Soraluce provide integrated solutions for manufacturing and maintenance.
The railway sector faces diverse and critical challenges that impact the efficiency, safety, and sustainability of rail transport. One of the key challenges is the need to develop durable components while maintaining high standards of strength and safety. In this regard we are working together with leading manufacturers to create new manufacturing and maintenance solutions that incorporate the latest technologies for applications such as axles, wheels, and bogies.
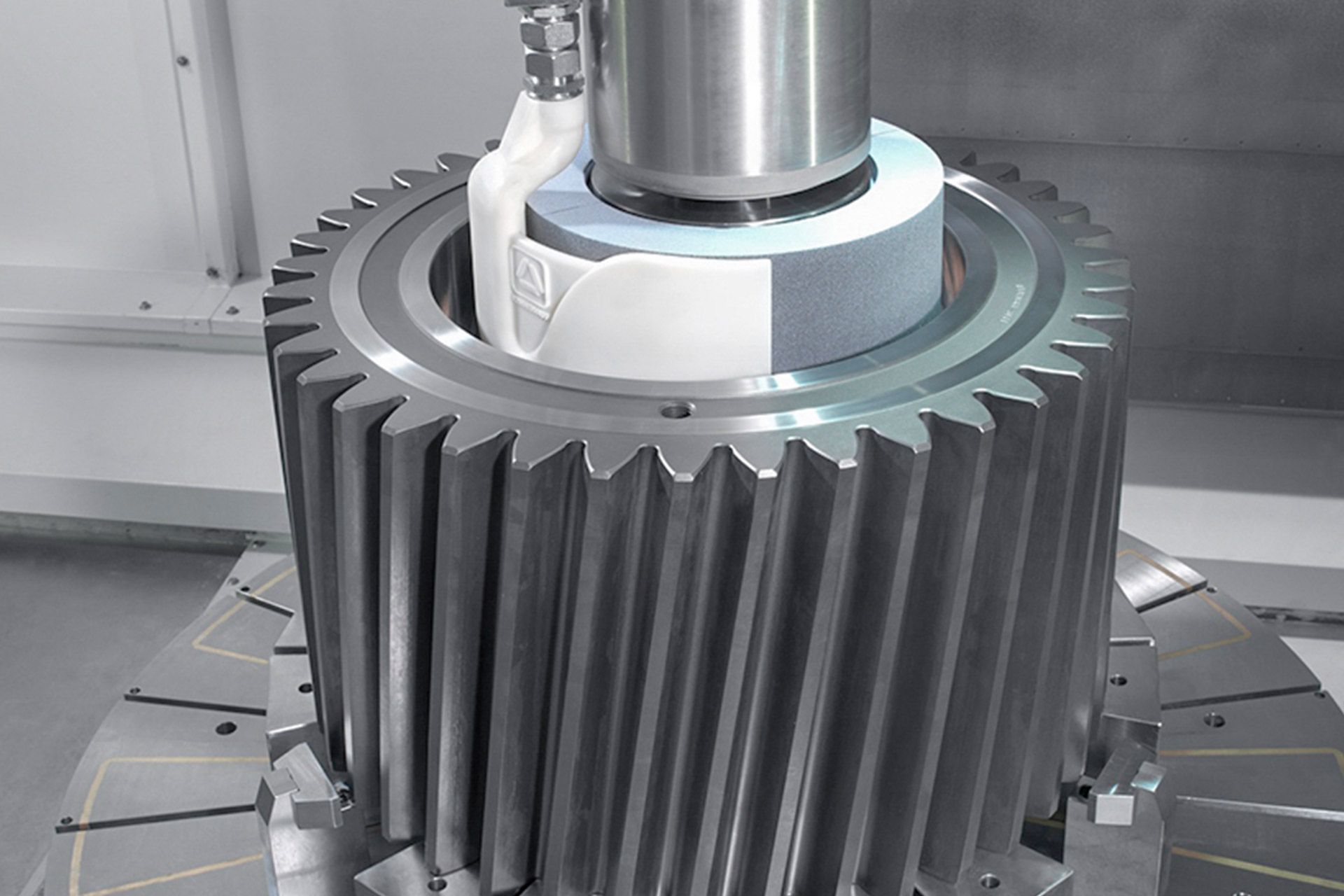
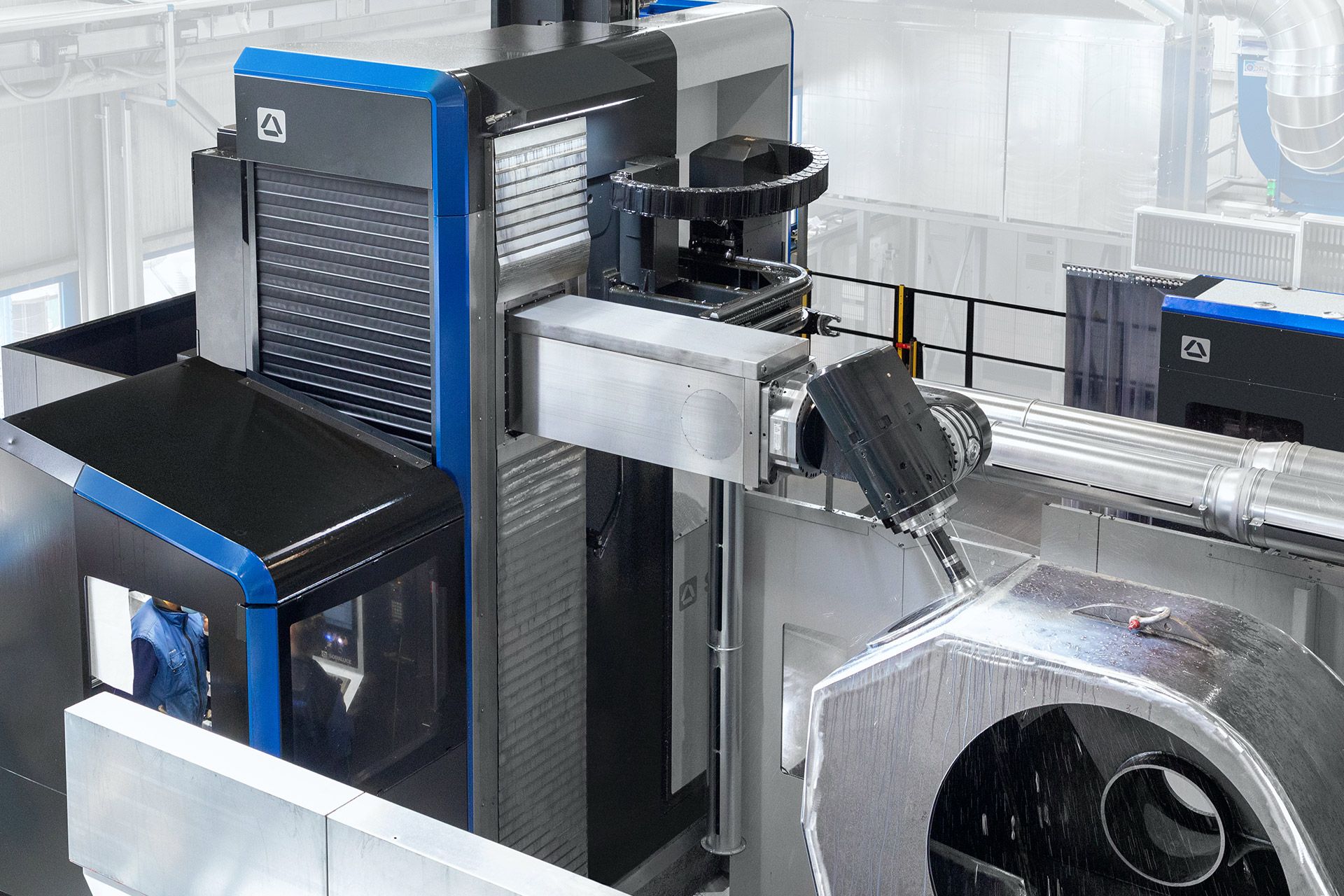
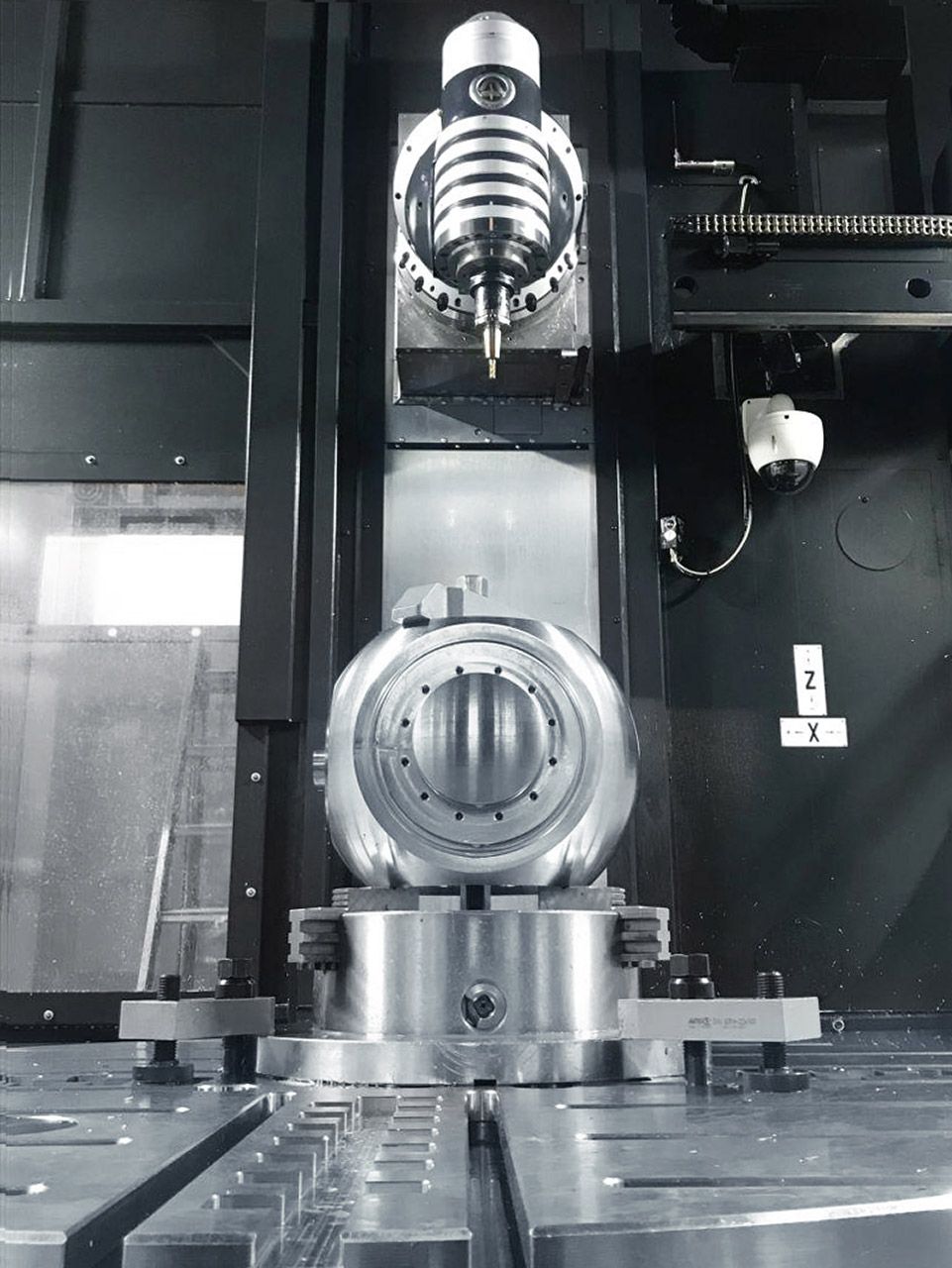
Energy
Danobat and Soraluce offer manufacturing solutions for various components in the energy sector, including renewable energy, hydropower, gas, and nuclear power.
We address specific challenges and requirements arising from the critical nature of equipment used in power generation, transmission, and distribution.
Our solutions demand high precision and stringent tolerances to ensure optimal performance and safety of components that often operate under extreme conditions.
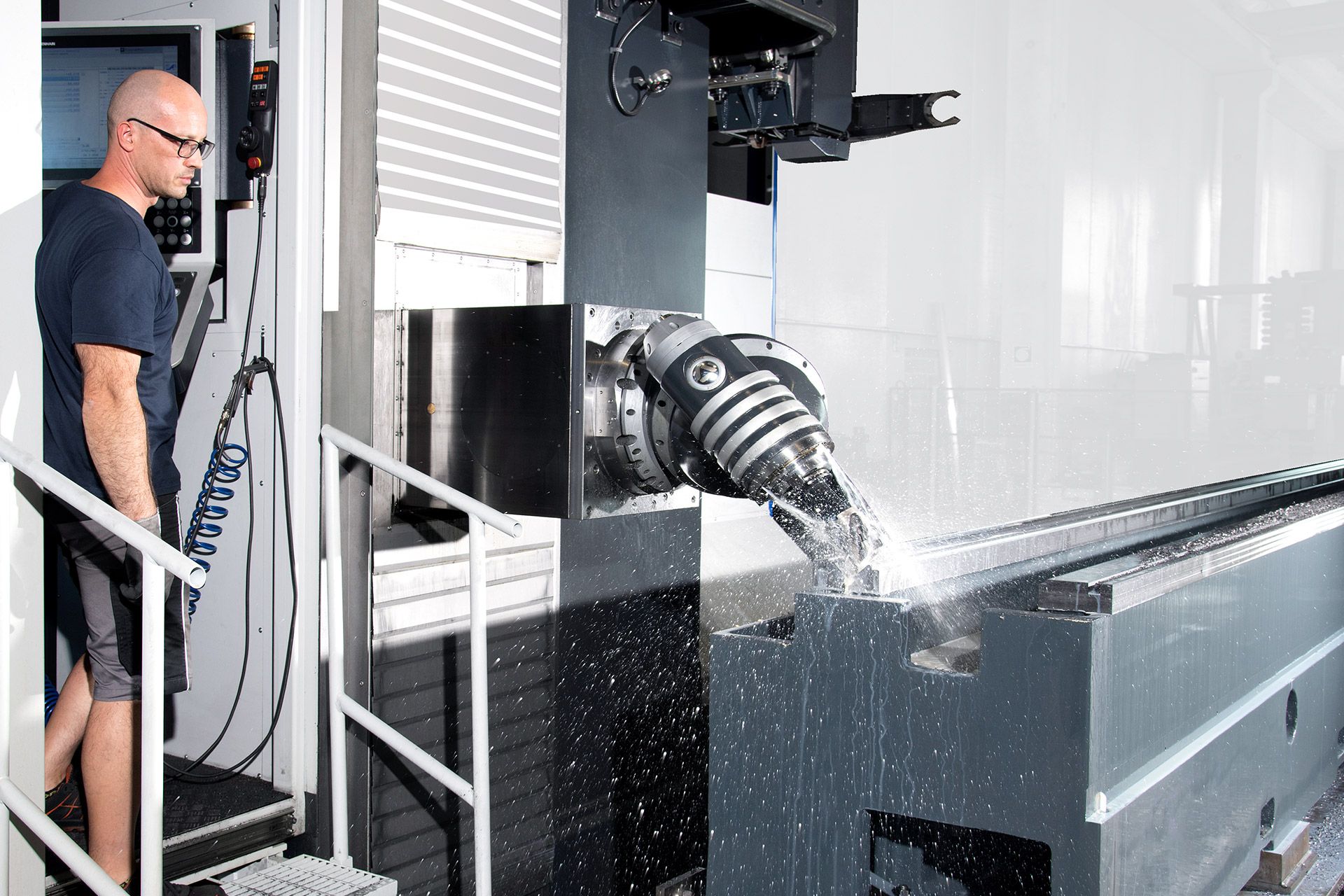
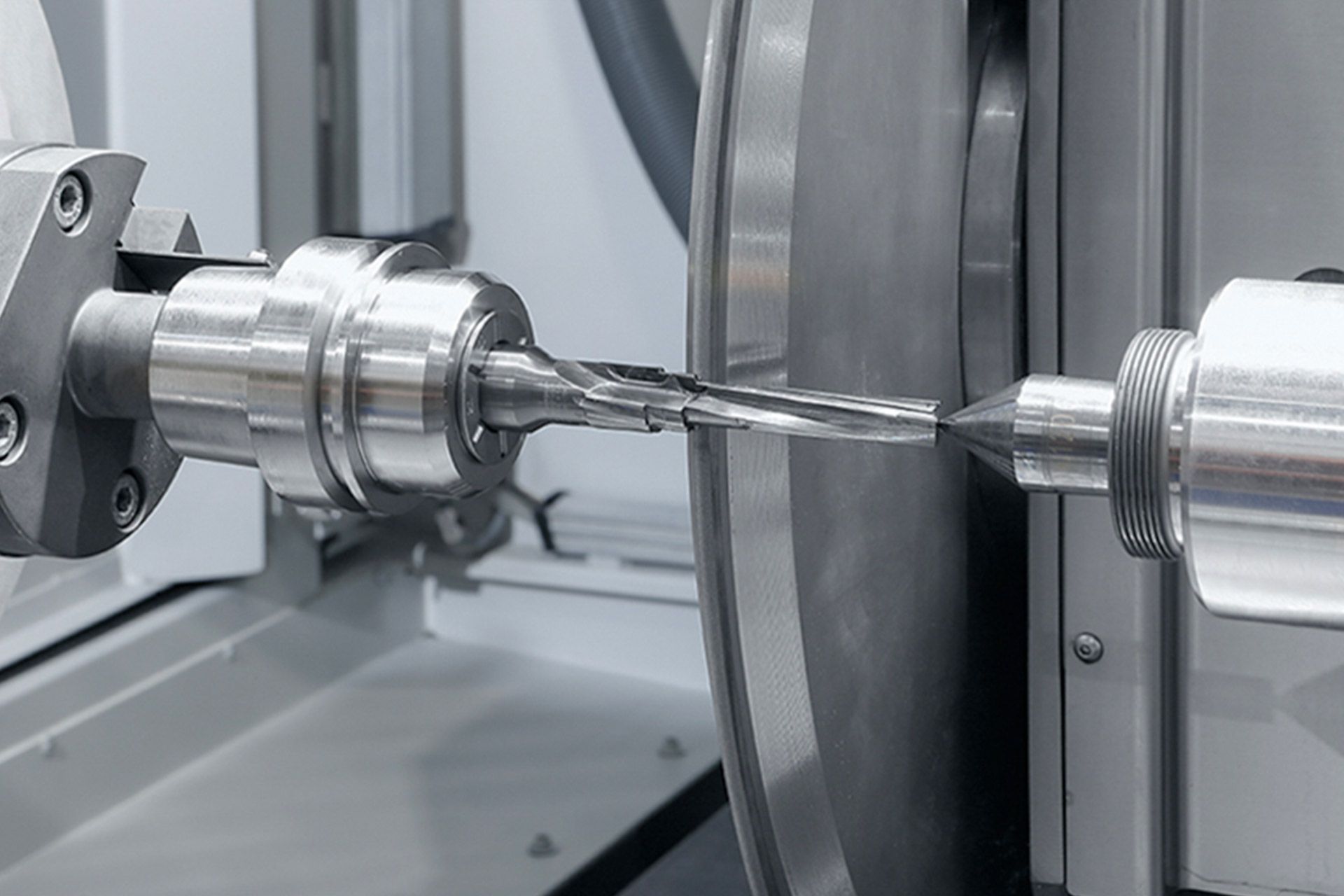
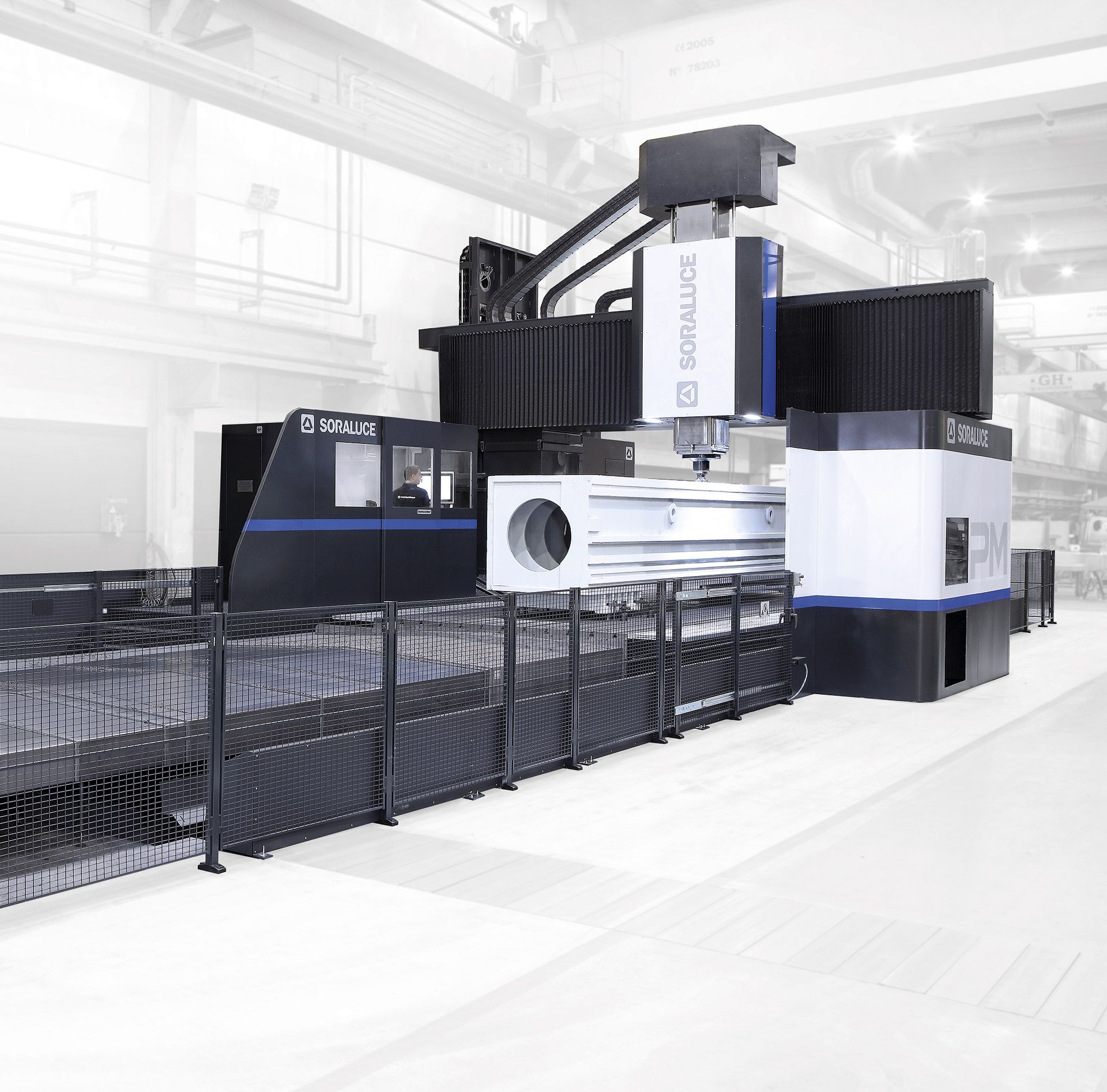
Capital goods
In a sector where production efficiency and quality are paramount, Danobat and Soraluce deliver advanced solutions for machining high-value-added components in diverse industries such as machine tools, agricultural machinery, mining equipment, food processing machinery, textile machinery, and metallurgical plant machinery.
Our ability to swiftly and seamlessly incorporate technological advances and adapt to emerging trends is crucial for successfully tackling the challenges in this sector.
Automation, turnkey lines and digital solutions
In addition to our core technologies, Danobatgroup companies extend a wide spectrum of customised end-to-end solutions, such as turnkey production lines, seamlessly integrated automation systems, and advanced digital services.
These solutions empower our customers to optimise operations, enhance efficiency, and fully harness the advantages of the digital age.
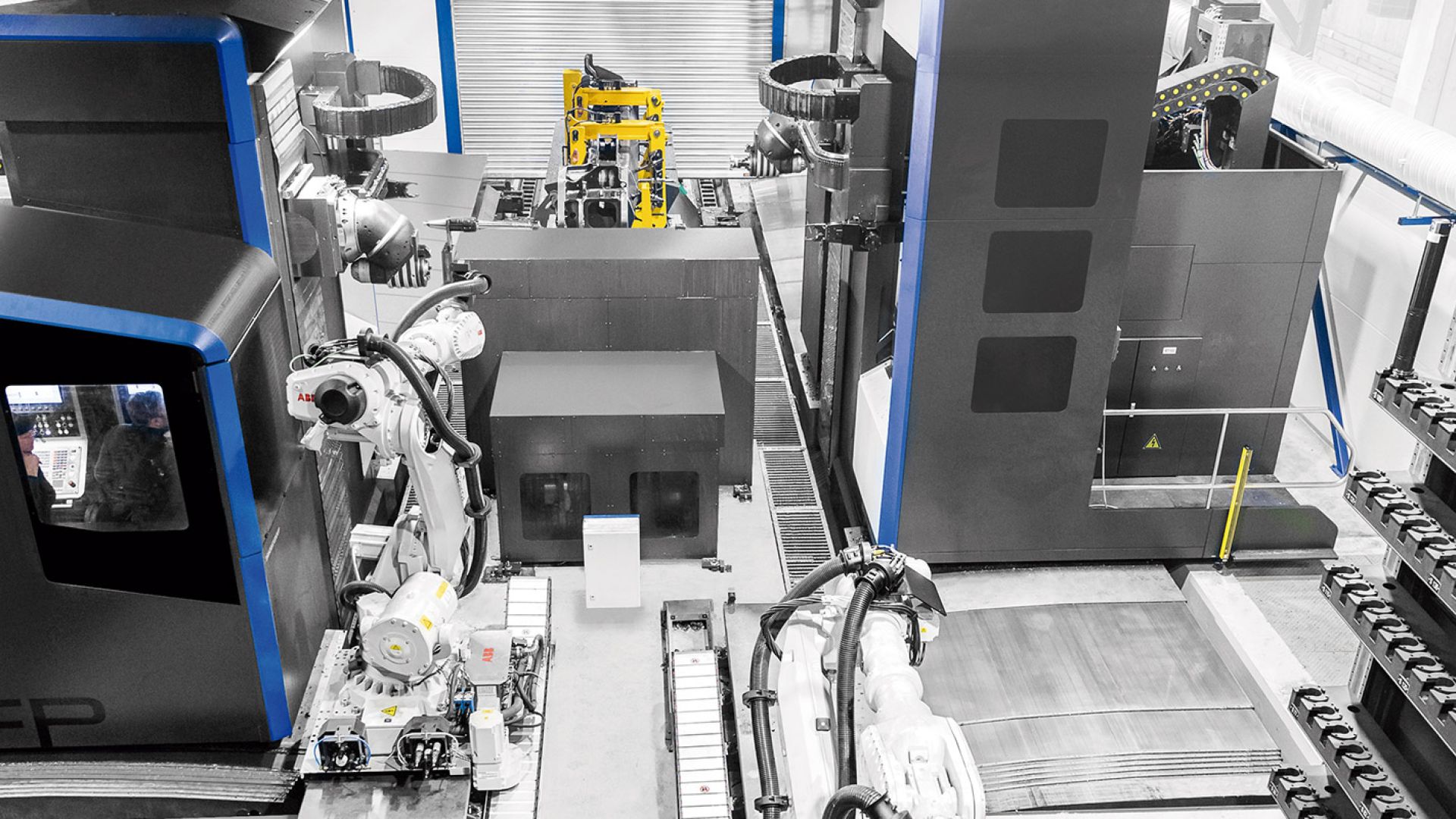
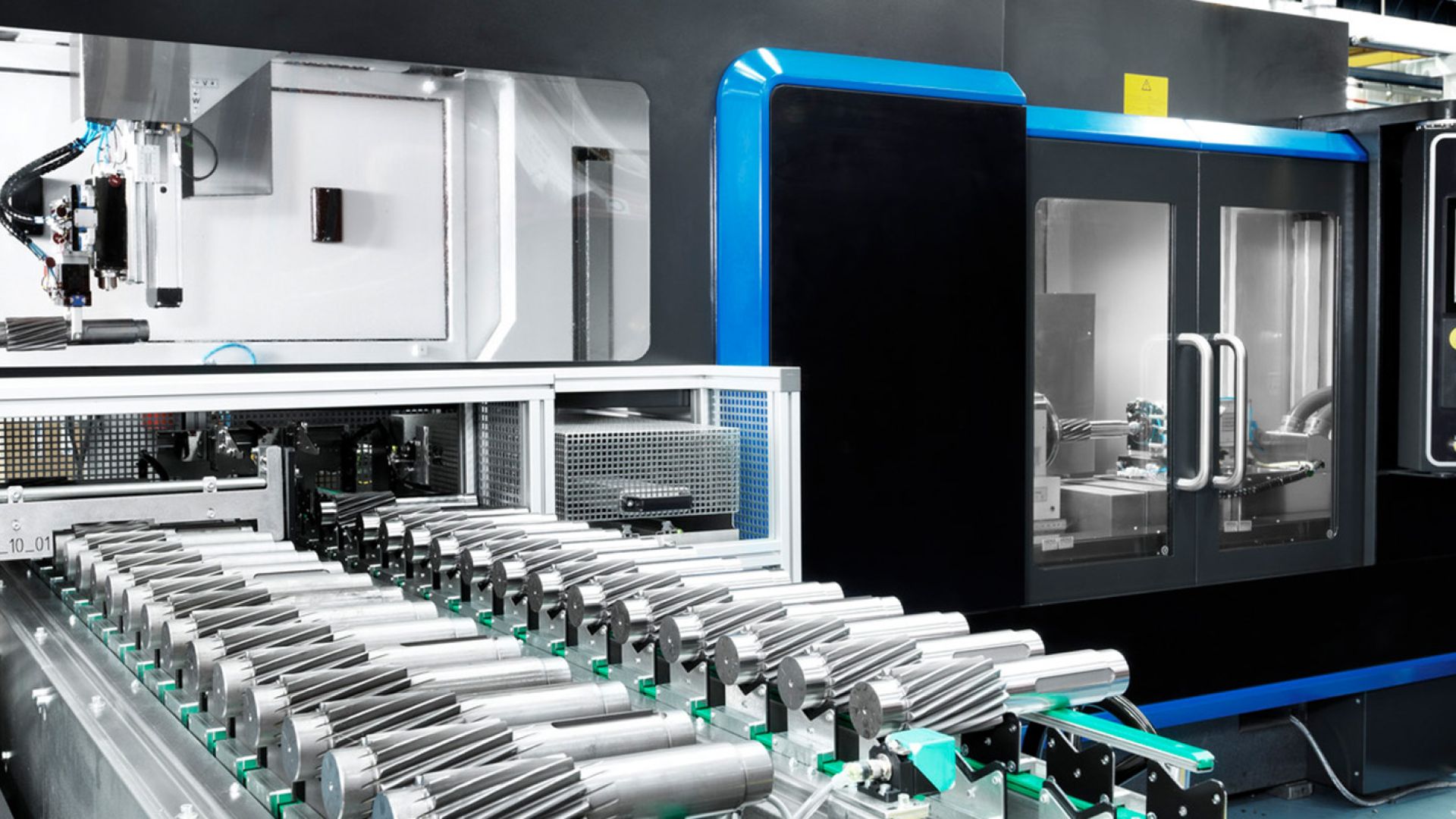
Projects that leave their mark
Distinguished by our unwavering commitment to embracing new challenges, our group companies consistently embark on extraordinary projects that redefine industry standards.
These projects broaden our horizons, open up new niches and enable us to create value across diverse sectors. Challenges that are the driving force behind our evolution, propelling us forward and reinforcing our growth. Together with our clients who stand as industry leaders, we forge the path towards ground-breaking achievements.
Discover our most recent flagship projects.
-
Blue Origin, a leading aerospace transportation company based in the USA, has incorporated an automated line comprising nine multitasking milling and turning centres for machining various rocket engine components, Inconel nozzles of the recoverable launchers, for its Blue Engine facility in Alabama.
The project developed by Soraluce is a customised solution, consisting of a palletised automated line that integrates nine milling-turning machines, with high torque 5 axis multitasking contouring head and milling-turning table.
Some of the main advantages of this solution are the optimisation and increase in production capacity, the reduction of part handling, greater precision in machining and the overall quality of the parts, as well as the reduction of production costs with improvements in the useful life of the tools and a reduction in machining cycle times.
-
Thanks to the collaboration with one of the largest mining companies in the world, Danobat has succeeded in finding a pioneering solution for the maintenance of freight wagons.
Characteristics of the project
Customer’s previous machining process:
- The process was not automatic
- Different flows, different entrance and output areas
Our solution:
- Automatic maintenance shop; main line for car first inspections and disassembly, bogie repair shop and a wheel shop maintaining around 30 ore cars per day
- Machine automatic programming based on customized CAM system
Advantages:
- Improved productivity
- Less workers are needed
- Fully automatic process, part flow automatically chooses, depending on the state of the wheelset
- The line is capable of managing changes bearings, wheels maintenance and installation of new wheelsets due to some element of the wheelset is damaged or end of life
- Reduction of ore car damage when they go from mines to the port
- Automatic centralized PLC system
- Increase safety and sustainability
The installations consist of:
- A line for ore car first inspection and disassembly
- Bogie repair shop
- Wheel shop maintenance equipment
- PECS central control system
-
Krones AG, German leading packaging and bottling machine manufacturer, has incorporated a large size Soraluce multitasking portal machine SORALUCE PR 6000 2T with two Ø 6000 mm milling-turning tables with high dree of automation, which includes a robotized tool magazine system with capability for 500 tools.
The machine, 32 m length, 14 m width and 300 tones, incorporates a good number of milling and turning heads to perform the required diverse machining operations and automatic head changing system. The process involves no downtime as it works in pendulum mode, loading/loading a workpiece in one station while the second station runs the machining process.
The project incorporated latest Soraluce Smart Technologies like DAS Damping Active Stabilizer or Adaptive Control.
-
Goimek worked together with SENER Aerospace on the JUICE -JUpiter ICy moons Explorer- mission, led by the European Space Agency (ESA), the aim of which was to explore the planet Jupiter and its three largest moons: Ganymede, Callisto and Europa.
Goimek was entrusted with the manufacturing of the MGAMA Medium Gain Antenna Main Assembly of the JUICE explorer. This two-axis steerable antenna operates in X- and Ka-bands and facilitates both the two-way communication between the spacecraft and Earth and the operation of the radio-frequency experiment carried by the probe.
Specifically, Goimek was in charge of manufacturing the main reflector, a titanium component with a thickness of 0.7mm, 500 mm in diameter and demanding exceptionally high-precision geometric tolerances, as well as the auxiliary elements necessary for the correct operation of the system: the struts and the sub-reflector.
Numerous facets had to be taken into account in the manufacture of these parts: from geometric intricacies, to ensure a correct operation of the mechanism, to the use of lightweight, cost-effective, yet resistant and durable materials to be able to withstand the harsh conditions of Jupiter’s icy moons.
In essence, the endeavour posed a significant challenge for Goimek, nonetheless one that has enabled the company to gain a deeper insight into this type of parts and to consolidate its market position as true specialists in precision machining for the aerospace sector.
Blue Origin, a leading aerospace transportation company based in the USA, has incorporated an automated line comprising nine multitasking milling and turning centres for machining various rocket engine components, Inconel nozzles of the recoverable launchers, for its Blue Engine facility in Alabama.
The project developed by Soraluce is a customised solution, consisting of a palletised automated line that integrates nine milling-turning machines, with high torque 5 axis multitasking contouring head and milling-turning table.
Some of the main advantages of this solution are the optimisation and increase in production capacity, the reduction of part handling, greater precision in machining and the overall quality of the parts, as well as the reduction of production costs with improvements in the useful life of the tools and a reduction in machining cycle times.
Thanks to the collaboration with one of the largest mining companies in the world, Danobat has succeeded in finding a pioneering solution for the maintenance of freight wagons.
Characteristics of the project
Customer’s previous machining process:
- The process was not automatic
- Different flows, different entrance and output areas
Our solution:
- Automatic maintenance shop; main line for car first inspections and disassembly, bogie repair shop and a wheel shop maintaining around 30 ore cars per day
- Machine automatic programming based on customized CAM system
Advantages:
Improved productivity
- Less workers are needed
- Fully automatic process, part flow automatically chooses, depending on the state of the wheelset
- The line is capable of managing changes bearings, wheels maintenance and installation of new wheelsets due to some element of the wheelset is damaged or end of life
- Reduction of ore car damage when they go from mines to the port
- Automatic centralized PLC system
- Increase safety and sustainability
The installations consist of:
- A line for ore car first inspection and disassembly
- Bogie repair shop
- Wheel shop maintenance equipment
- PECS central control system
Krones AG, German leading packaging and bottling machine manufacturer, has incorporated a large size Soraluce multitasking portal machine SORALUCE PR 6000 2T with two Ø 6000 mm milling-turning tables with high dree of automation, which includes a robotized tool magazine system with capability for 500 tools.
The machine, 32 m length, 14 m width and 300 tones, incorporates a good number of milling and turning heads to perform the required diverse machining operations and automatic head changing system. The process involves no downtime as it works in pendulum mode, loading/loading a workpiece in one station while the second station runs the machining process.
The project incorporated latest Soraluce Smart Technologies like DAS Damping Active Stabilizer or Adaptive Control.
Goimek worked together with SENER Aerospace on the JUICE -JUpiter ICy moons Explorer- mission, led by the European Space Agency (ESA), the aim of which was to explore the planet Jupiter and its three largest moons: Ganymede, Callisto and Europa.
Goimek was entrusted with the manufacturing of the MGAMA Medium Gain Antenna Main Assembly of the JUICE explorer. This two-axis steerable antenna operates in X- and Ka-bands and facilitates both the two-way communication between the spacecraft and Earth and the operation of the radio-frequency experiment carried by the probe.
Specifically, Goimek was in charge of manufacturing the main reflector, a titanium component with a thickness of 0.7mm, 500 mm in diameter and demanding exceptionally high-precision geometric tolerances, as well as the auxiliary elements necessary for the correct operation of the system: the struts and the sub-reflector.
Numerous facets had to be taken into account in the manufacture of these parts: from geometric intricacies, to ensure a correct operation of the mechanism, to the use of lightweight, cost-effective, yet resistant and durable materials to be able to withstand the harsh conditions of Jupiter’s icy moons.
In essence, the endeavour posed a significant challenge for Goimek, nonetheless one that has enabled the company to gain a deeper insight into this type of parts and to consolidate its market position as true specialists in precision machining for the aerospace sector.